Shoe with PU (polyurethane) borders and non-slip rubber outsole and method for preparing shoe
A rubber sole and rubber technology, applied in footwear, shoe soles, footwear, etc., can solve the problems of separation and low compatibility of interface polarity, and achieve high sole stiffness, high rubber density, and safe wearing The effect of increasing
- Summary
- Abstract
- Description
- Claims
- Application Information
AI Technical Summary
Problems solved by technology
Method used
Image
Examples
Embodiment 1
[0112] Embodiment 1 of the present invention: The rubber outsole formula is calculated in parts by weight and consists of the following two components: 40 parts of natural rubber, 40 parts of styrene-butadiene rubber, 20 parts of butadiene rubber, 1.8 parts of sulfur, and 3.6 parts of vulcanization accelerator agent, 6 parts of nano-zinc oxide, 2.5 parts of stearic acid, 15 parts of rubber softener, 48 parts of super wear-resistant carbon black, 0.2 part of anti-scorch agent, 1.0 part of release agent LTM-A, 2.4 parts of anti-aging agent. The formula of polyether polyurethane surround is calculated in parts by weight and consists of the following two components: Component 1: 96 parts of polytetrahydrofuran ether glycol, 0.8-1.2 parts of 101 silicone oil, 0.8-1.2 parts of distilled water, 1.5- 2.5 parts; 0.3-0.5 parts of triethylenediamine, 0.7-0.9 parts of ethylene glycol, 0.1-0.3 parts of UV-73P light absorber. Component two: 55-65 parts of polyethylene adipate, 35-45 parts o...
Embodiment 2
[0123] Embodiment 2 of the present invention: Outsole material: PU surrounds anti-slip rubber outsole shoe, and it comprises 40 parts of natural rubber, 50 parts of styrene-butadiene rubber, 10 parts of butadiene rubber, 1.9 parts of sulfur, 3.6 parts of vulcanization accelerator , 6 parts of nano zinc oxide, 2.5 parts of stearic acid, 15 parts of rubber softener, 48 parts of super wear-resistant carbon black. PU edge material: 96 parts of polytetrahydrofuran ether glycol, 1.1 parts of 101 silicone oil, 0.9 parts of distilled water, 2.1 parts of glycerol, 0.2 parts of UV-73P light absorber, 0.4 parts of triethylenediamine, and 0.8 parts of ethylene glycol. Get material A. 60 parts of polyethylene adipate, 40 parts of toluene diisocyanate.
[0124] The preparation method of the PU edge anti-slip rubber outsole shoes is the same as embodiment 1.
Embodiment 3
[0125] Embodiment 3 of the present invention: PU surrounds antiskid rubber outsole shoes, and rubber outsole it comprises 45 parts of natural rubbers, 40 parts of styrene-butadiene rubbers, 15 parts of butadiene rubbers, 1.8 parts of sulfur, 3.6 parts of vulcanization accelerators, 6 parts of nano zinc oxide, 2.5 parts of stearic acid, 14 parts of rubber softener, 49 parts of super wear-resistant carbon black. PU edge material: 96 parts of polytetrahydrofuran ether glycol, 1.0 parts of 101 silicone oil, 0.9 parts of distilled water, 1.9 parts of glycerol, 0.2 parts of UV-73P light absorber, 0.3 parts of triethylenediamine, and 0.9 parts of ethylene glycol. Get material A. 60 parts of polyethylene adipate, 40 parts of toluene diisocyanate.
[0126] The preparation method of the PU edge anti-slip rubber outsole shoes is the same as embodiment 1.
PUM
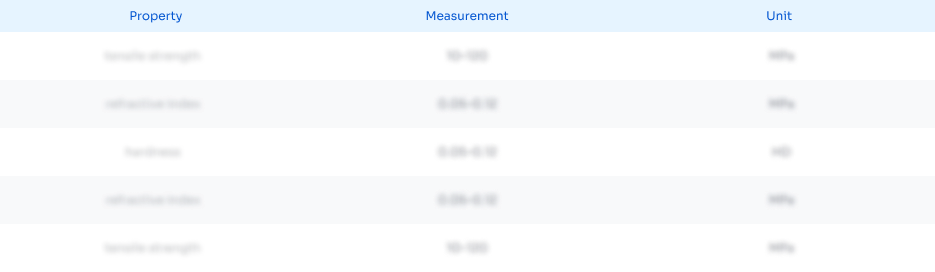
Abstract
Description
Claims
Application Information

- R&D Engineer
- R&D Manager
- IP Professional
- Industry Leading Data Capabilities
- Powerful AI technology
- Patent DNA Extraction
Browse by: Latest US Patents, China's latest patents, Technical Efficacy Thesaurus, Application Domain, Technology Topic, Popular Technical Reports.
© 2024 PatSnap. All rights reserved.Legal|Privacy policy|Modern Slavery Act Transparency Statement|Sitemap|About US| Contact US: help@patsnap.com