Preparation method of linear thermal-reversible polyurethane polymer with flame retardancy and polymer
A technology of polyurethane polymer and flame retardant performance, which is applied in the field of polymer material synthesis and preparation, can solve the problems of complex synthesis process, etc., and achieve the effect of simple preparation method, good flame retardancy and short preparation cycle
- Summary
- Abstract
- Description
- Claims
- Application Information
AI Technical Summary
Problems solved by technology
Method used
Examples
Embodiment 1
[0024] Add 30g of polytetrahydrofuran ether diol (PTMG-1000) with a relative number average molecular weight of 1000 and 3.66g of tetrachlorobisphenol A into a 250ml three-necked flask, melt and stir at 80°C for 25min; then add 9.80g of 4,4-bisphenol Phenylmethane diisocyanate (MDI), stirred rapidly for 5min. Finally, the mixture was aged in a vacuum oven at 80° C. for 5 hours, and then slowly cooled to room temperature to obtain a linear thermoreversible polyurethane polymer with flame retardancy. According to the infrared test under heating and cooling, the synthesized polymer has thermal reversible behavior at about 100°C; and the flame retardant performance test is carried out according to the measurement standard of GB 2406-80 limiting oxygen index, and the limiting oxygen index of the polymer can reach 27.5.
[0025] The molar ratio of polyols and halogenated bisphenol chain extenders is 3:1;
[0026] The NCO to OH molar ratio is 0.98:1.
Embodiment 2
[0028] Add 30g of polytetrahydrofuran ether diol (PTMG-1000) and 8.16g of tetrabromobisphenol A in a 250ml three-necked flask with a relative number average molecular weight of 1000, melt and stir at 90°C for 15min; then add 7.83g of toluene diisocyanate ( TDI-100), stirring rapidly for 3min. Finally, the mixture was aged in a vacuum oven at 85° C. for 4.5 hours, and then slowly cooled to room temperature to obtain a linear thermoreversible polyurethane polymer with flame-retardant properties. According to the infrared test under heating and cooling, the synthesized polymer has thermally reversible behavior at around 95°C; and the flame retardant performance test is carried out according to the measurement standard of GB 2406-80 limiting oxygen index, and the limiting oxygen index of the polymer can reach 29.
[0029] The molar ratio of polyols and halogenated bisphenol chain extenders is 2:1;
[0030] NCO and OH molar ratio is 1:1.
Embodiment 3
[0032] Add 30g of poly-1,4-butylene adipate diol (PBA-1000) with a relative number average molecular weight of 1000 and 5.44g of tetrabromobisphenol A into a 250ml three-necked flask, melt and stir for 30min at 70°C ; Then add 6.89g toluene diisocyanate (TDI-100), and stir rapidly for 4min. Finally, the mixture was aged in a vacuum oven at 90° C. for 3.5 hours, and then slowly cooled to room temperature to obtain a linear thermoreversible polyurethane polymer with flame-retardant properties. According to the infrared test under heating and cooling, the synthesized polymer has thermal reversible behavior at about 95°C; and the flame retardant performance test is carried out according to the measurement standard of GB 2406-80 limiting oxygen index, and the limiting oxygen index of the polymer can reach 30.
[0033] The molar ratio of polyols and halogenated bisphenol chain extenders is 3:1;
[0034] The NCO and OH molar ratio is 0.99:1.
PUM
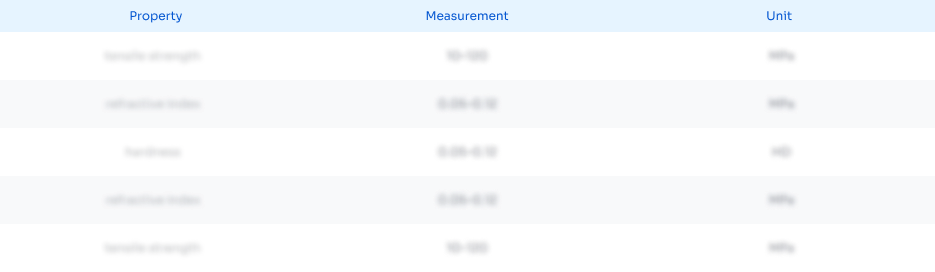
Abstract
Description
Claims
Application Information

- R&D
- Intellectual Property
- Life Sciences
- Materials
- Tech Scout
- Unparalleled Data Quality
- Higher Quality Content
- 60% Fewer Hallucinations
Browse by: Latest US Patents, China's latest patents, Technical Efficacy Thesaurus, Application Domain, Technology Topic, Popular Technical Reports.
© 2025 PatSnap. All rights reserved.Legal|Privacy policy|Modern Slavery Act Transparency Statement|Sitemap|About US| Contact US: help@patsnap.com