Modified latex masterbatch/styrene butadiene rubber foam material
A technology of styrene-butadiene rubber and foaming materials, which is applied in the field of rubber foaming materials, can solve problems such as increasing the difficulty of industrial production, high requirements for foaming equipment, and complicated processes, and achieves better mechanical strength, simple preparation methods, and The effect of process simplification
- Summary
- Abstract
- Description
- Claims
- Application Information
AI Technical Summary
Problems solved by technology
Method used
Image
Examples
Embodiment 1
[0033] Preparation of modified styrene-butadiene latex masterbatch 1-2
[0034] (1) Get 20g of white carbon black and 40g of blowing agent AC and mix evenly, add in 100ml of absolute ethanol, ultrasonic treatment for 40min, prepare the white carbon black / AC dispersion liquid;
[0035] (2) Get 20ml of white carbon black / AC dispersion liquid and join in the styrene-butadiene latex of 80ml, at room temperature mechanically vigorously stir 30min, obtain uncured modified styrene-butadiene latex,
[0036] (3) Pour the uncured modified styrene-butadiene latex into a mold, put it into a drying oven at 60° C. for curing, granulate after curing, and dry to obtain the modified styrene-butadiene latex masterbatch 1-2.
Embodiment 2
[0038] Preparation of modified styrene-butadiene latex masterbatch 1-11
[0039] (1) Get 20g of white carbon black, 20g of blowing agent AC, and 20g of blowing agent OBSH and mix evenly, add it to 100ml of absolute ethanol, and ultrasonically treat it for 40min to prepare a white carbon black / AC / OBSH dispersion;
[0040] (2) Get 20ml of white carbon black / AC / OBSH dispersion liquid and join in the styrene-butadiene latex of 80ml, at room temperature mechanically vigorously stir 30min, obtain uncured modified styrene-butadiene latex;
[0041] (3) Pour the uncured modified styrene-butadiene latex into a mold, put it into a drying oven at 60°C for curing, granulate after curing, and dry to obtain the modified styrene-butadiene latex masterbatch 1-11.
Embodiment 3
[0043] Preparation of modified natural latex masterbatch 1-21
[0044] (1) Get 20g of white carbon black, 40g of blowing agent AC, and 20g of blowing agent OBSH, mix evenly, add it to 100ml of absolute ethanol, and ultrasonically treat it for 40min to prepare a white carbon black / AC / OBSH dispersion;
[0045] (2) Get 20ml of white carbon black / AC / OBSH dispersion liquid and join in the natural latex of 80ml, at room temperature, mechanically vigorously stir 30min, obtain uncured modified natural latex;
[0046] (3) Pour the uncured modified natural latex into a mold, put it into a drying oven at 60°C for curing, granulate after curing, and dry to obtain the modified natural latex masterbatch 1-21.
PUM
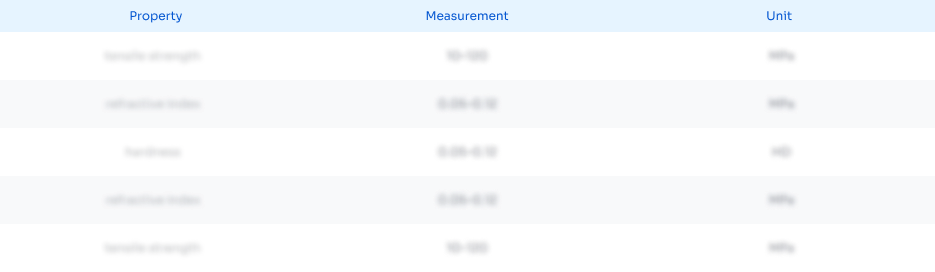
Abstract
Description
Claims
Application Information

- R&D Engineer
- R&D Manager
- IP Professional
- Industry Leading Data Capabilities
- Powerful AI technology
- Patent DNA Extraction
Browse by: Latest US Patents, China's latest patents, Technical Efficacy Thesaurus, Application Domain, Technology Topic, Popular Technical Reports.
© 2024 PatSnap. All rights reserved.Legal|Privacy policy|Modern Slavery Act Transparency Statement|Sitemap|About US| Contact US: help@patsnap.com