Application of viscosity reducing type polycarboxylate superplasticizer in preparation of tailing sand concrete
A technology of viscous polycarboxylate and concrete, which is applied in the field of preparation of tailings sand concrete and viscosity-reducing polycarboxylate superplasticizer, which can solve the problems of large void ratio, poor water retention, rough surface, etc.
- Summary
- Abstract
- Description
- Claims
- Application Information
AI Technical Summary
Problems solved by technology
Method used
Image
Examples
Embodiment 1
[0063] The preparation method of the viscosity-reducing polycarboxylate water reducer of the present invention, the preparation method comprises the following steps:
[0064] (1) Synthesis of viscosity-reducing active macromonomer D:
[0065] In a four-necked glass flask equipped with a stirrer, a thermometer, a reflux condenser, and a dropping device, add 1 mol of methallyl alcohol, 2 g of sodium hydride, stir under nitrogen protection, and drop 30 mol of ring The oxyalkane was added dropwise in 3 hours, and the reaction was continued at 100°C for 8 hours to obtain the viscosity-reducing active macromonomer D.
[0066] (2) Synthesis of viscosity-reducing polycarboxylate superplasticizer
[0067] Dissolving reactive monomer B, reactive monomer C, reactive monomer D, and oxidizing agent in water to obtain solution 1, dissolving reactive monomer A and chain transfer agent in water to obtain solution 2, dissolving reducing agent in water to obtain solution 3, Under normal tempe...
Embodiment 2
[0071] The preparation method of the viscosity-reducing polycarboxylate water reducer of the present invention, the preparation method comprises the following steps:
[0072] (1) Synthesis of viscosity-reducing active macromonomer D:
[0073] In a four-necked glass flask equipped with a stirrer, a thermometer, a reflux condenser, and a dropping device, add 1 mol of methallyl alcohol and 2 g of sodium hydride, stir under nitrogen protection, and add 30 mol dropwise at a constant speed at 90 ° C. , Ethyl 3-epoxy 3-phenylpropionate was added dropwise in 3 hours, and the reaction was continued at 100°C for 8 hours to obtain the viscosity-reducing active macromonomer D.
[0074] (2) Synthesis of viscosity-reducing polycarboxylate superplasticizer
[0075] Dissolving reactive monomer B, reactive monomer C, reactive monomer D, and oxidizing agent in water to obtain solution 1, dissolving reactive monomer A and chain transfer agent in water to obtain solution 2, dissolving reducing a...
Embodiment 3
[0079] The preparation method of the viscosity-reducing polycarboxylate water reducer of the present invention, the preparation method comprises the following steps:
[0080] (1) Synthesis of viscosity-reducing active macromonomer D:
[0081] In a four-necked glass flask equipped with a stirrer, a thermometer, a reflux condenser, and a dropping device, add 1 mol of methallyl alcohol, 2 g of sodium hydride, stir under nitrogen protection, and dropwise add 15 mol of ring Oxyalkane and 15mol ethyl 2,3 epoxy 3-phenylpropionate were added dropwise in 3 hours, and the reaction was continued at 100°C for 8 hours to obtain the viscosity-reducing active macromonomer D.
[0082] (2) Synthesis of viscosity-reducing polycarboxylate superplasticizer
[0083] Dissolving reactive monomer B, reactive monomer C, reactive monomer D, and oxidizing agent in water to obtain solution 1, dissolving reactive monomer A and chain transfer agent in water to obtain solution 2, dissolving reducing agent ...
PUM
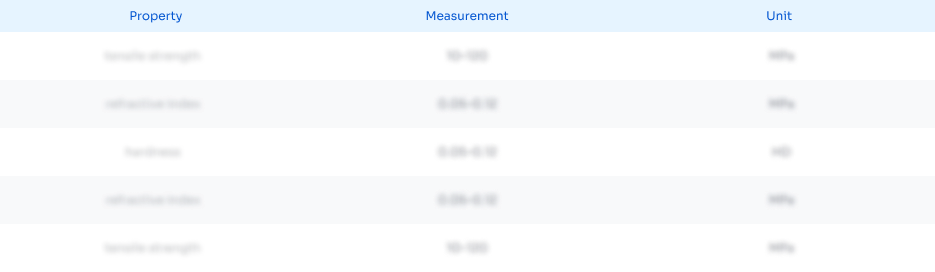
Abstract
Description
Claims
Application Information

- R&D
- Intellectual Property
- Life Sciences
- Materials
- Tech Scout
- Unparalleled Data Quality
- Higher Quality Content
- 60% Fewer Hallucinations
Browse by: Latest US Patents, China's latest patents, Technical Efficacy Thesaurus, Application Domain, Technology Topic, Popular Technical Reports.
© 2025 PatSnap. All rights reserved.Legal|Privacy policy|Modern Slavery Act Transparency Statement|Sitemap|About US| Contact US: help@patsnap.com