Preparation method of selective emitter of solar cell
A solar cell and selective technology, applied in circuits, photovoltaic power generation, electrical components, etc., can solve the problems affecting the performance of solar cells and high surface concentration, and achieve the effect of low surface concentration, simple process, shallow junction and deep junction
- Summary
- Abstract
- Description
- Claims
- Application Information
AI Technical Summary
Problems solved by technology
Method used
Image
Examples
Embodiment 1
[0044] This embodiment provides a method for preparing a selective emitter of a solar cell, using a silicon oxide film with a thickness of 1.5 nm and a polysilicon film with a thickness of 200 nm as the doped filter layer, which specifically includes the following steps.
[0045] Step 101, using HCl+H 2 O 2 The solution and hydrofluoric acid clean the P-type silicon substrate 1 after texturing;
[0046] Step 102, using low pressure chemical vapor deposition (LPCVD) to sequentially grow a layer of silicon oxide film 2 with a thickness of 1.5 nm and a layer of polysilicon film 3 with a thickness of 200 nm on the entire surface of the cleaned silicon substrate 1 (the growth temperature is 610℃), that is, the silicon oxide film 2 is located between the polysilicon film 3 and the silicon substrate 1, such as figure 1 Shown
[0047] Step 103, according to the pattern design of the metal contact electrode, use a picosecond laser to remove the silicon oxide film 2 and the polysilicon film 3 ...
Embodiment 2
[0053] This embodiment provides a method for preparing a selective emitter of a solar cell, which uses a silicon oxide film with a thickness of 0.5 nm and a microcrystalline silicon film with a thickness of 300 nm as the doped filter layer, which specifically includes the following steps.
[0054] Step 201, using HCl+H 2 O 2 Solution and hydrofluoric acid clean the N-type silicon substrate after texturing;
[0055] Step 202, using plasma-enhanced chemical vapor deposition (PECVD) to sequentially grow a layer of silicon oxide film with a thickness of 0.5 nm and a layer of microcrystalline silicon film with a thickness of 300 nm on the entire surface of the cleaned silicon substrate (the growth temperature is 600℃), that is, the silicon oxide film is located between the microcrystalline silicon film and the silicon substrate;
[0056] Step 203, according to the pattern design of the metal contact electrode, use a picosecond laser to remove the silicon oxide film and the microcrystallin...
Embodiment 3
[0062] This embodiment provides a method for preparing a selective emitter of a solar cell, which uses a silicon oxide film with a thickness of 2.5 nm and an amorphous silicon film with a thickness of 500 nm as the doped filter layer, which specifically includes the following steps.
[0063] Step 301, using HCl+H 2 O 2 Solution and hydrofluoric acid clean the N-type silicon substrate after texturing;
[0064] Step 302, using low pressure chemical vapor deposition (LPCVD) to sequentially grow a silicon oxide film with a thickness of 2.5 nm and an amorphous silicon film with a thickness of 500 nm (growth temperature is 590) on the entire surface of the cleaned silicon substrate. °C), that is, the silicon oxide film is located between the amorphous silicon film and the silicon substrate;
[0065] Step 303, according to the pattern design of the metal contact electrode, use a picosecond laser to remove the silicon oxide film and the amorphous silicon film on the metal contact area on the...
PUM
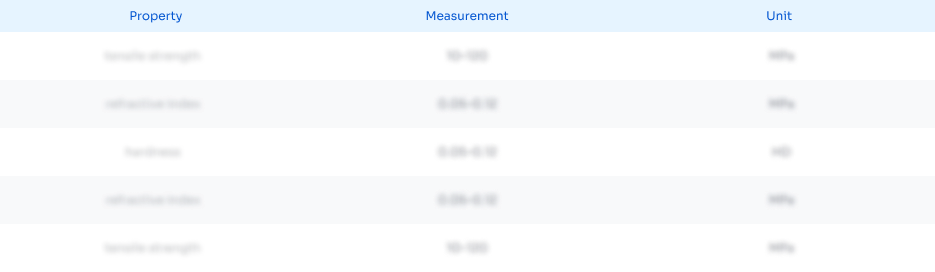
Abstract
Description
Claims
Application Information

- R&D
- Intellectual Property
- Life Sciences
- Materials
- Tech Scout
- Unparalleled Data Quality
- Higher Quality Content
- 60% Fewer Hallucinations
Browse by: Latest US Patents, China's latest patents, Technical Efficacy Thesaurus, Application Domain, Technology Topic, Popular Technical Reports.
© 2025 PatSnap. All rights reserved.Legal|Privacy policy|Modern Slavery Act Transparency Statement|Sitemap|About US| Contact US: help@patsnap.com