A method for automatic nozzle deburring and flow adjustment
A flow regulation and deburring technology, which is applied in metal processing equipment, used abrasive processing devices, manufacturing tools, etc., can solve the problem of flow stability, aero-engine safety, lack of good removal methods, poor consistency, etc. problems, to achieve the effect of good consistency, complete removal of burrs, and high efficiency of flow regulation
- Summary
- Abstract
- Description
- Claims
- Application Information
AI Technical Summary
Problems solved by technology
Method used
Image
Examples
Embodiment Construction
[0028] The present invention will be further described in detail below in conjunction with the accompanying drawings and specific embodiments.
[0029] A method for automatic nozzle deburring and flow adjustment, comprising the following steps:
[0030] Step 1: Detect the initial flow of the nozzle through the special detection equipment for nozzle flow, and record the initial flow values of the main fuel injection port 3 and the auxiliary fuel injection port 4 respectively;
[0031] Step 2: Use abrasive flow equipment to process the main oil circuit of the nozzle, first connect the main oil inlet 1 with the abrasive flow output port of the abrasive flow equipment, and then press figure 1 The flow direction shown is to feed the water-based abrasive flow into the nozzle, and the flow direction of the water-based abrasive flow in the nozzle needs to be consistent in one direction, and the burrs on the main oil road of the nozzle are removed by the water-based abrasive flow; th...
PUM
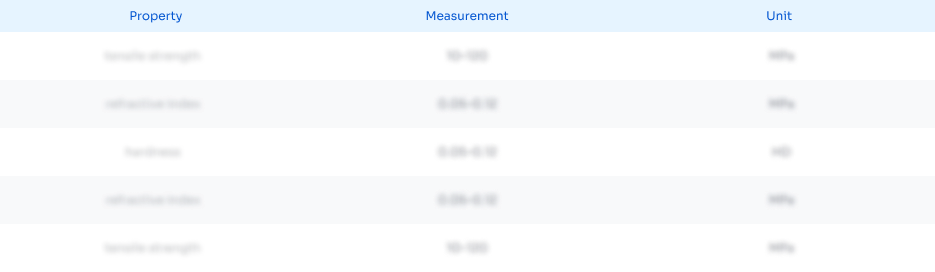
Abstract
Description
Claims
Application Information

- R&D
- Intellectual Property
- Life Sciences
- Materials
- Tech Scout
- Unparalleled Data Quality
- Higher Quality Content
- 60% Fewer Hallucinations
Browse by: Latest US Patents, China's latest patents, Technical Efficacy Thesaurus, Application Domain, Technology Topic, Popular Technical Reports.
© 2025 PatSnap. All rights reserved.Legal|Privacy policy|Modern Slavery Act Transparency Statement|Sitemap|About US| Contact US: help@patsnap.com