High-assembling-rate steel tube concrete frame structure system and connecting method
A technology of steel pipe concrete and frame structure, which is applied to truss structures, building structures, joists, etc., and can solve the problems of heavy installation work and low assembly efficiency, so as to prevent potential safety hazards, improve efficiency, and increase the docking area Effect
- Summary
- Abstract
- Description
- Claims
- Application Information
AI Technical Summary
Problems solved by technology
Method used
Image
Examples
Embodiment 1
[0055] A high-assembly-rate concrete-filled steel tube frame structure system according to the present invention includes concrete columns 1 composed of steel pipes and concrete, composite beams 2 composed of semi-open steel boxes and concrete, concrete slabs 3, and column-to-column flange connection nodes , beam-column joints, post-cast concrete on site, where:
[0056] The lower part of the side wall of the concrete column 1 is penetrated with a reinforced steel sleeve 6, and the wall thickness of the reinforced steel sleeve 6 is greater than that of the concrete column 1 and protrudes 300-500mm from the floor; the lower part of the side wall of the concrete column 1 and the side of the reinforced steel sleeve 6 The walls are provided with a through hole 7 and a through hole 8; the through hole 7 and the through hole 8 are respectively penetrated with an anchor bar 9 in the column and a first tie anchor bolt 10; the concrete column 1 and the reinforced steel sleeve 6 first pa...
Embodiment 2
[0062] A connection method for a high assembly rate concrete-filled steel tube frame structure system, the specific steps are as follows:
[0063] Step 1. Fix the reinforced steel sleeve 6
[0064] The reinforced steel sleeve 6 is penetrated through the lower part of the concrete column 1, the bottom of the reinforced steel sleeve 6 is 10-20mm higher than the bottom of the concrete column 1, and the through hole 7 and the through hole 8 are opened, and the anchor bar (9) and the second A tie anchor bolt 10 runs through the through hole 7 and the through hole 8 respectively, and the two ends of the anchor bar 9 in the column are folded into a 90° hook with a special tool, and the required concrete column 1 is subjected to this treatment in turn, Leave a concrete column 1 not pierced with anchor bar 9 in the column for subsequent use;
[0065] Step 2. Connect the flange
[0066] The upper flange 4 and the lower flange 5 are respectively welded to the upper and lower ends of th...
PUM
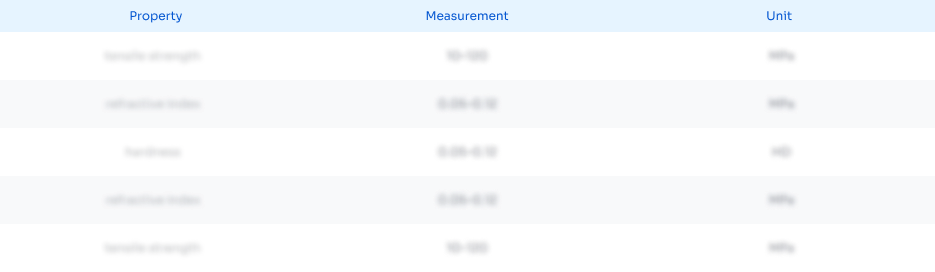
Abstract
Description
Claims
Application Information

- Generate Ideas
- Intellectual Property
- Life Sciences
- Materials
- Tech Scout
- Unparalleled Data Quality
- Higher Quality Content
- 60% Fewer Hallucinations
Browse by: Latest US Patents, China's latest patents, Technical Efficacy Thesaurus, Application Domain, Technology Topic, Popular Technical Reports.
© 2025 PatSnap. All rights reserved.Legal|Privacy policy|Modern Slavery Act Transparency Statement|Sitemap|About US| Contact US: help@patsnap.com