Aerial vehicle structure
A technology of vehicle and skeleton structure, which is applied in the direction of superstructure sub-assembly, connection between superstructure sub-assemblies, building components, etc. or voids, etc., to facilitate handling and assembly, improve strength and stability, and maintain structural integrity
- Summary
- Abstract
- Description
- Claims
- Application Information
AI Technical Summary
Problems solved by technology
Method used
Image
Examples
Embodiment 1
[0052] Such as figure 1 Shown: a kind of aircraft, its fuselage 1 comprises fuselage, wing and empennage, and wherein fuselage comprises fuselage skin 11 and is located at the first bulkhead 12 of fuselage skin 11 inner cavity, girder 13. The wing includes a wing skin 14 and a longitudinal wall 15 located in the inner cavity of the wing skin. The bottom of the aircraft includes a floor 16, a fuselage skin 11, a second partition frame 17 and a beam 18 arranged in the inner cavity of the fuselage skin.
[0053] Wherein, the fuselage skin 11, the wing skin 14, the longitudinal wall 15, and the floor 16 are all made of metal plates. Wherein, the fuselage skin 11 and the wing skin 14 are made of arc-shaped metal plates. The vertical walls 15 and the floor 16 are made of sheet metal of planar construction.
[0054] Adjacent metal plates and between metal plates and other parts of the body can be connected by means of welding, screwing or the like.
[0055] Such as figure 2 or ...
Embodiment 2
[0063] On the basis of Embodiment 1, the first bulkhead 222, the girder 223, the second bulkhead 227 and the cross beam 228 are also made of metal plates. Wherein the first frame 222 and the second frame 227 are welded by a plurality of arc-shaped metal plates, and the truss 223 and the cross beam 228 are both made of plane metal plates. The second bulkhead 227 and the beam 228 are welded into one body and reinforced by bolts.
[0064] The skeleton structure of this embodiment is made of metal plates, which not only ensures the strength but also improves the light weight.
Embodiment 3
[0066] On the basis of Embodiment 1, the seats in the aircraft are also made of sheet metal.
[0067] The backrest of the seat is a metal plate with a curved structure, while the seat is a metal plate with a planar structure.
PUM
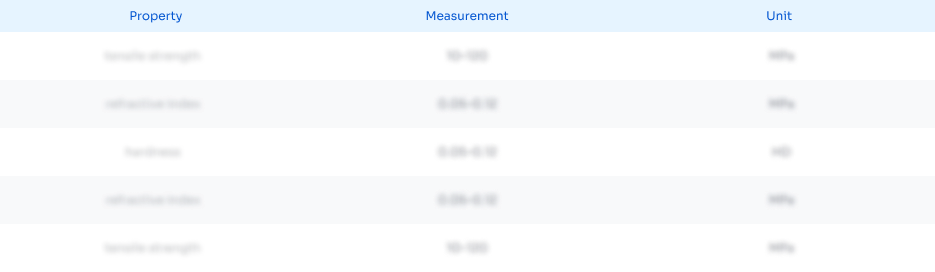
Abstract
Description
Claims
Application Information

- R&D
- Intellectual Property
- Life Sciences
- Materials
- Tech Scout
- Unparalleled Data Quality
- Higher Quality Content
- 60% Fewer Hallucinations
Browse by: Latest US Patents, China's latest patents, Technical Efficacy Thesaurus, Application Domain, Technology Topic, Popular Technical Reports.
© 2025 PatSnap. All rights reserved.Legal|Privacy policy|Modern Slavery Act Transparency Statement|Sitemap|About US| Contact US: help@patsnap.com