Container floor and machining method thereof
A processing method and container technology, which are applied in wood processing appliances, sugarcane machining, manufacturing tools, etc., can solve the problems of high production time and cost, high price, long growth cycle, etc., to control production costs, reduce production costs, time saving effect
- Summary
- Abstract
- Description
- Claims
- Application Information
AI Technical Summary
Problems solved by technology
Method used
Image
Examples
Embodiment 1
[0025] A container floor processing method, comprising the following steps:
[0026] a. Prepare arc-shaped bamboo slice unit: select 3-5 years old raw bamboo, cut off the head and tail to make bamboo poles; then select the part with a diameter of more than 8cm of bamboo poles, and cut the bamboo tubes with a length less than 2500mm; then the bamboo tubes 3-6 equal parts are divided proportionally, and the inner and outer segments are removed to obtain arc-shaped bamboo unit;
[0027] b. Preparation of long rectangular bamboo slice units: flatten the arc-shaped bamboo slice units by rolling and high-speed planing to make long rectangular units with uniform thickness and loose density; the line speed of planing and drawing treatment should not be lower than 10m / min;
[0028] c. Integralization: The long rectangular bamboo unit is integrated by weaving to form a whole long rectangular bamboo unit
[0029] d. drying treatment: the whole long rectangular bamboo chip unit is dried ...
Embodiment 2
[0036] Based on Example 1, step g in a container floor processing method undergoes three hot-press curing treatments; the first hot-press curing treatment: the unit pressure is 2.5-3.5MPa, the temperature is 135-145°C, and the time is 30-40min; The second hot pressing curing treatment: the unit pressure is 1.0-2.0MPa, the temperature is 135-145°C, and the time is 10-15min; the third hot pressing curing treatment: the unit pressure is 0.5Mpa, the temperature is 110-135°C, and the time is 10 minutes -15min.
PUM
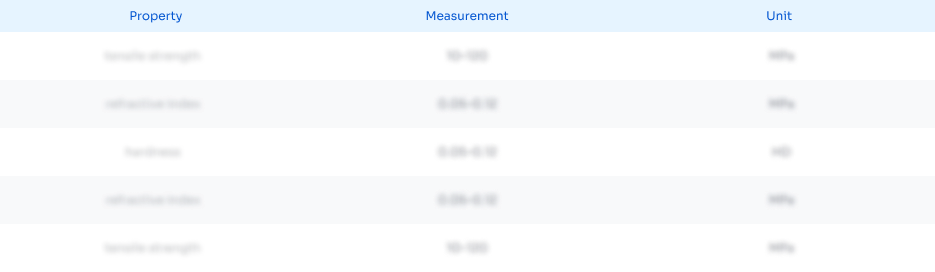
Abstract
Description
Claims
Application Information

- R&D
- Intellectual Property
- Life Sciences
- Materials
- Tech Scout
- Unparalleled Data Quality
- Higher Quality Content
- 60% Fewer Hallucinations
Browse by: Latest US Patents, China's latest patents, Technical Efficacy Thesaurus, Application Domain, Technology Topic, Popular Technical Reports.
© 2025 PatSnap. All rights reserved.Legal|Privacy policy|Modern Slavery Act Transparency Statement|Sitemap|About US| Contact US: help@patsnap.com