Method for converting methane into aliphatic hydrocarbons, fuel cell and fuel cell preparation method
A fuel cell, aliphatic hydrocarbon technology, applied in the direction of fuel cells, battery electrodes, circuits, etc., can solve the problems of poor safety and low selectivity of aliphatic hydrocarbons, and achieve improved safety, reduced membrane area, and fast oxygen supply rate. Effect
- Summary
- Abstract
- Description
- Claims
- Application Information
AI Technical Summary
Problems solved by technology
Method used
Image
Examples
preparation example Construction
[0042] The present invention also discloses a method for preparing the above-mentioned fuel cell, and the preparation steps specifically include:
[0043] S1, the oxygen ion conductor type ceramic material powder is screened and then cold-pressed into tablets;
[0044] S2. Sintering the rough sheet prepared in S1 at high temperature to obtain a dense electrolyte sheet;
[0045] S3, mixing the cathode material and the electrolyte material powder, making slurry, coating one side of the electrolyte sheet in S2, and sintering at a high temperature to obtain an electrolyte-cathode transition layer;
[0046] S4, mixing the cathode material powder and the pore-forming agent, making slurry, coating the surface of the transition layer in S3, and sintering at a high temperature to obtain a porous cathode layer;
[0047] S5. Mixing the methane oxidative coupling catalyst and the inert conductive material to slurry and coating it on the other side of the electrolyte sheet in S2, and sint...
Embodiment 1
[0061] Barium carbonate catalyst was prepared by solution method: 7.415g magnesium nitrate Mg(NO 3 ) 2 (Sigma-Aldrich, product number 237175-100G, purity ≥ 99%) and 11.267g barium oxalate BaC 2 o 4 (Alfa Aesar, product number 13009, purity ≥ 99.999%) powder ground, poured into 100mL deionized water to prepare a mixed solution. After the solid powder is completely dispersed, heat at 80°C to concentrate and evaporate the liquid to obtain a uniformly mixed solid powder. The dry powder was placed in a muffle furnace and sintered in air at 800 °C for 4 hours to prepare MgO / BaCO 3 It is a methane oxidative coupling catalyst.
Embodiment 2
[0063] Preparation of lanthanum aluminum oxide catalyst by solution method: 4.33g lanthanum nitrate La(NO 3 ) 3 *6H 2 O (Sigma-Aldrich, product number 61520-100G-F, purity ≥ 99%), 3.375g aluminum nitrate Al (NO 3 ) 3 *9H 2 O (Sima-Aldrich, product number 237973-500G, purity ≥ 98%) and 0.256g magnesium nitrate Mg (NO 3 ) 2 *6H 2 O (Sigma-Aldrich, product number 237175-100G, purity ≥ 99%) powder was fully ground, poured into 100mL 0.5M citric acid aqueous solution to dissolve. After the solid is fully dissolved, gradually concentrate at 80°C and 100°C until the liquid evaporates completely. The evaporated powder was collected and transferred to a muffle furnace, the temperature was gradually raised to 800°C and air sintered for 5 hours to prepare a LaAlMgO-based methane oxidative coupling catalyst.
PUM
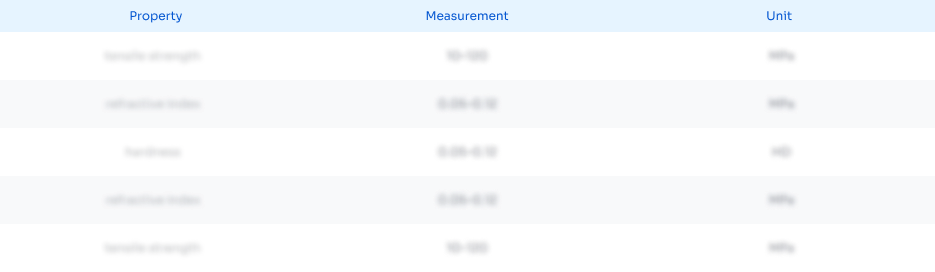
Abstract
Description
Claims
Application Information

- R&D
- Intellectual Property
- Life Sciences
- Materials
- Tech Scout
- Unparalleled Data Quality
- Higher Quality Content
- 60% Fewer Hallucinations
Browse by: Latest US Patents, China's latest patents, Technical Efficacy Thesaurus, Application Domain, Technology Topic, Popular Technical Reports.
© 2025 PatSnap. All rights reserved.Legal|Privacy policy|Modern Slavery Act Transparency Statement|Sitemap|About US| Contact US: help@patsnap.com