Forging process of GH4169 alloy bar
A GH4169, 1. GH4169 technology, applied in the forging process field of GH4169 alloy rods, can solve the problems that the grain size difference has not been well resolved, the control of the grain size difference needs to be improved, and the grain size is refined. Achieve the effect of improving the internal quality of the billet and the uniformity of grain size
- Summary
- Abstract
- Description
- Claims
- Application Information
AI Technical Summary
Problems solved by technology
Method used
Image
Examples
Embodiment 1
[0029] The φ508 electroslag ingot is subjected to homogenization heat treatment, kept at 1150°C for 1 hour, and forged on a 45MN fast forging machine for 5 times, three upsetting and three pulling out. Put it into a heating furnace at 1100°C for solid solution treatment, and keep it warm for 1.5 hours; the second upsetting deformation is 55%, and the length is drawn first, and the edge can be lightly chamfered during the drawing process, and the deformation is controlled at 14% to 35%. , into a heating furnace at 1100°C for solid solution treatment, and held for 2 hours; the third upsetting deformation is 50% to 60%. %, the third elongation is completed with two fires, the penultimate heat is solution treated at 1100°C for 1.5h, and the last fire is heated at 1050°C for 1h. The quick-forging intermediate billet is air-cooled, turned and rounded, and then sent to a heating furnace at 1050±10°C for solution treatment for 2 hours. Finally, the intermediate billet is sent to the ...
PUM
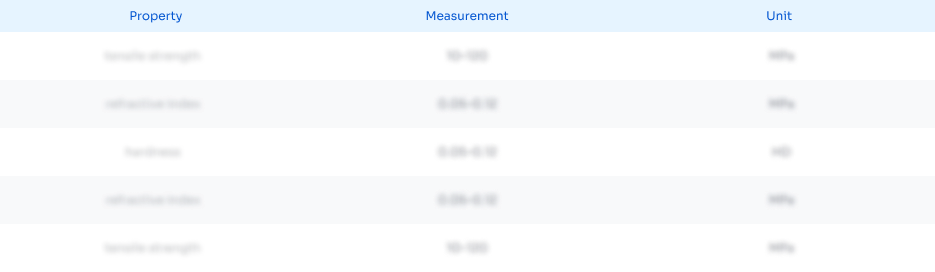
Abstract
Description
Claims
Application Information

- R&D
- Intellectual Property
- Life Sciences
- Materials
- Tech Scout
- Unparalleled Data Quality
- Higher Quality Content
- 60% Fewer Hallucinations
Browse by: Latest US Patents, China's latest patents, Technical Efficacy Thesaurus, Application Domain, Technology Topic, Popular Technical Reports.
© 2025 PatSnap. All rights reserved.Legal|Privacy policy|Modern Slavery Act Transparency Statement|Sitemap|About US| Contact US: help@patsnap.com