Preparation method of machine air filter paper
A technology of machine air filter paper and solution, applied in the field of filter paper, can solve the problem of resin protective layer falling off, and achieve the effect of high removal rate, enhanced adsorption effect, high activity and adsorption performance
- Summary
- Abstract
- Description
- Claims
- Application Information
AI Technical Summary
Problems solved by technology
Method used
Examples
Embodiment 1
[0030] The preparation method of modified coral reef powder:
[0031]After crushing the coral reef, roast it at a high temperature of 250° C. for 4 hours to obtain coral reef particles, and set aside; add the salvianolic acid extract to a 70% ethanol aqueous solution to prepare a solution with a concentration of 7 wt % salvianolic acid extract, and prepare the coral reef particles Add the salvianolic acid extract solution with the epoxy silane coupling agent at a mass ratio of 1:0.3, the mass ratio of coral reef particles to the salvianolic acid extract is 1:4, and stir and react at 58°C for 4.5h. After filtering, washing with water and drying, the modified coral reef powder is obtained.
[0032] Preparation method of base paper:
[0033] a) mixing reed pulp, loofah fiber, and bamboo fiber for beating, the mass ratio of reed pulp, loofah fiber, and bamboo fiber is 1:0.35:3, and diluted with water to form a slurry 1 with a concentration of 2.2wt%;
[0034] b) Add modified cor...
Embodiment 2
[0042] The preparation method of modified coral reef powder:
[0043] After the coral reef is crushed, it is roasted at a high temperature of 210°C for 2.5h to obtain coral reef particles, and it is set aside; the salvianolic acid extract is added to a 70% ethanol aqueous solution to prepare a 6wt% salvianolic acid extract solution, and the coral reef The particles and epoxy silane coupling agent were added into the salvianolic acid extract solution at a mass ratio of 1:0.2, the mass ratio of coral reef particles to salvianolic acid extract was 1:3, and stirred and reacted at 56°C for 3.5h , filtered, washed with water, and dried to obtain the modified coral reef powder.
[0044] Preparation method of base paper:
[0045] a) mixing reed pulp, loofah fiber, and bamboo fiber for beating, the mass ratio of reed pulp, loofah fiber, and bamboo fiber is 1:0.25:3, and diluted with water to form a slurry 1 with a concentration of 2.1wt%;
[0046] b) Add modified coral reef powder an...
Embodiment 3
[0054] The preparation method of modified coral reef powder:
[0055] After crushing the coral reef, roast it at a high temperature of 270° C. for 5 hours to obtain coral reef particles, which are set aside; add the salvianolic acid extract to a 70% ethanol aqueous solution to prepare a solution with a concentration of 8 wt % salvianolic acid extract, and prepare the coral reef particles Add the salvianolic acid extract solution with the epoxy silane coupling agent at a mass ratio of 1:0.4, the mass ratio of the coral reef particles to the salvianolic acid extract is 1:4, stir and react at 58°C for 5h, after Filter, wash with water, and dry to obtain the modified coral reef powder.
[0056] Preparation method of base paper:
[0057] a) mixing reed pulp, loofah fiber, and bamboo fiber for beating, the mass ratio of reed pulp, loofah fiber, and bamboo fiber is 1:0.4:4, and diluted with water to form a slurry 1 with a concentration of 2.5wt%;
[0058] b) Add modified coral reef...
PUM
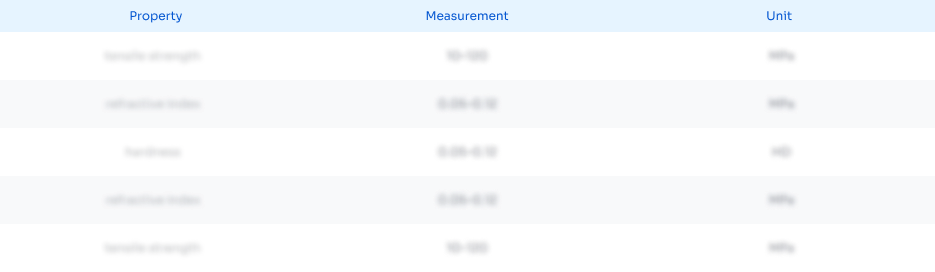
Abstract
Description
Claims
Application Information

- R&D
- Intellectual Property
- Life Sciences
- Materials
- Tech Scout
- Unparalleled Data Quality
- Higher Quality Content
- 60% Fewer Hallucinations
Browse by: Latest US Patents, China's latest patents, Technical Efficacy Thesaurus, Application Domain, Technology Topic, Popular Technical Reports.
© 2025 PatSnap. All rights reserved.Legal|Privacy policy|Modern Slavery Act Transparency Statement|Sitemap|About US| Contact US: help@patsnap.com