Textile yarn oiling machine
A textile yarn and oil machine technology, which is applied in the field of textile yarn processing, can solve problems such as oil pollution, easy adhesion, and affecting yarn quality, and achieve the effects of improving spinnability, activity, and quality
- Summary
- Abstract
- Description
- Claims
- Application Information
AI Technical Summary
Problems solved by technology
Method used
Image
Examples
Embodiment Construction
[0029] Compared with the traditional dip-dyeing oiling device, the present invention improves on the above-mentioned three major defects in the background technology to solve the defects in the prior art, and makes the dip-dyeing oiling machine reach a higher technical height.
[0030] like Figure 1-9 The shown oiling machine for textile yarns includes a dip-dyeing oiling device 1 and a spring-type oiling device 2 located on one side of the dipping-dyeing oiling device 1. The oiling device for oiling the yarn 0 has an oil container containing the oil 24. The spring-type degreasing device 2 is used to remove the excess oil 24 entrained on the yarn 0 after dipping. 2. Remove excess oil 24 by vibrating the yarn 0. Yarn 0 passes through the dip-dyeing oiling device 1 and the spring-type oiling device 2 sequentially along the conveying direction, that is to say, the yarn 0 passes through the dip-dyeing oiling device 1 and then passes through the spring-type oiling device 2 Exce...
PUM
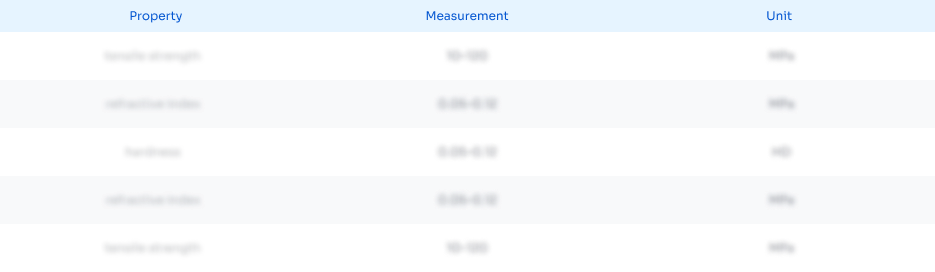
Abstract
Description
Claims
Application Information

- R&D Engineer
- R&D Manager
- IP Professional
- Industry Leading Data Capabilities
- Powerful AI technology
- Patent DNA Extraction
Browse by: Latest US Patents, China's latest patents, Technical Efficacy Thesaurus, Application Domain, Technology Topic, Popular Technical Reports.
© 2024 PatSnap. All rights reserved.Legal|Privacy policy|Modern Slavery Act Transparency Statement|Sitemap|About US| Contact US: help@patsnap.com