Method for improving bagasse enzymolysis efficiency through delignification pretreatment and addition of additive
A technology of enzymatic hydrolysis efficiency and pretreatment, applied in fermentation and other directions, can solve the problems of increasing the cost of glucose production, long enzymatic hydrolysis time, etc., and achieve the effect of shortening enzymatic hydrolysis time, improving enzymatic hydrolysis efficiency and improving efficiency.
- Summary
- Abstract
- Description
- Claims
- Application Information
AI Technical Summary
Problems solved by technology
Method used
Image
Examples
Embodiment 1
[0027] Weigh 50g of absolutely dry bagasse raw material into a triangular flask, add 500ml of distilled water and 5g of NaOH, place it on a constant temperature shaker, set the speed to 150 rpm, and react for 12 hours at room temperature 25℃. After finishing, immediately The pretreatment residue is separated by vacuum filtration. The analysis of the pretreatment residue showed that the removal rates of hemicellulose and lignin reached 31.6% and 10.6%, respectively, and their effects on the glucose yield in the enzymatic hydrolysis section were as follows figure 1 Shown.
[0028] Take 5 grams (calculated on the absolute dry basis) of the pretreatment residue, add 100 FPU cellulase (Saili second generation), 0.75 grams Tween 80 and 250 mL acetic acid-sodium acetate buffer solution with pH=4.8 for enzymatic hydrolysis. During the enzymolysis process, the temperature is controlled at 50°C and the rotation speed is 150 rpm. After 24 hours of enzymatic hydrolysis, 1 mL of enzymatic h...
Embodiment 2
[0030] Weigh 50g of absolutely dry bagasse raw material and place it in a triangular flask, add 500ml of distilled water and 5g of NaOH, place it on a constant temperature shaker at a speed of 150 rpm, heat it to quickly increase the temperature to 60℃ and start timing, wait for the reaction When the time reaches 4 hours, the heating is stopped, and the reaction is immediately reduced to room temperature with condensed water, and the pretreatment residue is separated by vacuum filtration. The analysis of the pretreatment residue shows that the removal rates of hemicellulose and lignin reached 36.1% and 24.2%, respectively, and their influence on the glucose yield in the enzymatic hydrolysis section is as follows figure 1 Shown.
[0031] Take 5 grams (calculated on the absolute dry basis) of the pretreatment residue, add 100 FPU cellulase (Saili second generation), 0.75 grams Tween 80 and 250 mL acetic acid-sodium acetate buffer solution with pH=4.8 for enzymatic hydrolysis. Duri...
Embodiment 3
[0033] Weigh 50g of absolutely dry bagasse material and place it in a closed reactor equipped with a thermocouple, add 500ml of distilled water and 5g of NaOH, turn on the stirring, heat to quickly increase the temperature to 120°C and start timing, wait until the reaction time reaches 2 hours , Stop heating, and immediately lower the reaction to room temperature with condensed water, and use vacuum filtration to separate the pretreatment residue. The analysis of the pretreatment residue showed that the removal rates of hemicellulose and lignin reached 46% and 40.1%, respectively, and their effects on the glucose yield in the enzymatic hydrolysis section were as follows: figure 1 Shown.
[0034] Take 5 grams (calculated on the absolute dry basis) of the pretreatment residue, add 100 FPU cellulase (Saili second generation), 0.75 grams Tween 80 and 250 mL acetic acid-sodium acetate buffer solution with pH=4.8 for enzymatic hydrolysis. During the enzymolysis process, the temperatur...
PUM
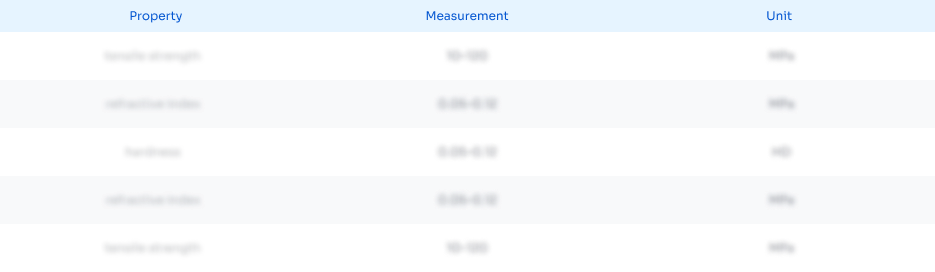
Abstract
Description
Claims
Application Information

- R&D
- Intellectual Property
- Life Sciences
- Materials
- Tech Scout
- Unparalleled Data Quality
- Higher Quality Content
- 60% Fewer Hallucinations
Browse by: Latest US Patents, China's latest patents, Technical Efficacy Thesaurus, Application Domain, Technology Topic, Popular Technical Reports.
© 2025 PatSnap. All rights reserved.Legal|Privacy policy|Modern Slavery Act Transparency Statement|Sitemap|About US| Contact US: help@patsnap.com