A method for recovering NdFeB casing sludge waste by ca-chloride reduction diffusion technology
A technology for recycling NdFeB and NdFeB, which is applied to the improvement of process efficiency, transportation and packaging, metal processing equipment, etc., which can solve the problem of increasing the secondary use and waste of resources, reducing the efficiency of waste recycling, and not considering the use of calcium and other issues, to achieve the effect of environmentally friendly resource recycling, resource conservation, and resource recycling
- Summary
- Abstract
- Description
- Claims
- Application Information
AI Technical Summary
Problems solved by technology
Method used
Image
Examples
Embodiment 1
[0020] Take 50g of NdFeB casing sludge and dry it in a blast drying oven at 60°C for 10 hours, and then disperse it by grinding after drying; add 15g of metal calcium particles and 27.8g of potassium chloride to the ground sludge powder, and dry it at 950°C , insulated under an argon atmosphere for 2 hours; the product obtained was soaked in water at 2°C for 30 minutes, and the powder was initially selected with a magnet; the obtained magnetic powder was ultrasonically cleaned with 5vol.% dilute acetic acid for 10 minutes, and then the powder was washed with distilled water until The pH value of the solution is about 8, and finally washed once with alcohol; the cleaned powder is dried in a vacuum environment, and the oxygen content of the dried powder is about 3800ppm; after drying, prevent contact with air and place it directly in a glove box with an argon atmosphere Medium; powder doped with 30wt.% Nd 4 Fe 14 The B alloy powder is rotated in a rolling ball mill for 1.5h, or...
Embodiment 2
[0022] Take 50g of NdFeB bushing sludge and dry it in a blast drying oven at 80°C for 15 hours, and then disperse it by grinding after drying; add 18g of metal calcium particles and 35g of potassium chloride to the ground sludge powder, and dry it at 830°C, Insulate for 2 hours under an argon atmosphere; soak the obtained product in water at 5°C for 60 minutes, and use a magnet to initially select the powder; ultrasonically clean the obtained magnetic powder with 10vol.% dilute acetic acid for 15 minutes, and then wash the powder with distilled water to a solution The pH value is about 8, and finally washed once with alcohol; the cleaned powder is dried in a vacuum environment, and the oxygen content of the dried powder is about 3000ppm; after drying, prevent contact with air and place it directly in a glove box with an argon atmosphere ;Powder doped with 35wt.% Nd 3 PrFe 14 The B alloy powder is rotated in a rolling ball mill for 1.5h, oriented and pressed in a nitrogen atmo...
Embodiment 3
[0024] Take 50g of NdFeB casing sludge and dry it in a blast drying oven at 100°C for 20 hours. After drying, it is dispersed by grinding; the grinded sludge powder is added with 20g of metal calcium particles and 50g of potassium chloride, and dried at 1150°C, Insulate for 2 hours under an argon atmosphere; soak the obtained product in water at 5°C for 90 minutes, and use a magnet to initially select the powder; ultrasonically clean the obtained magnetic powder with 15vol.% dilute acetic acid for 15 minutes, and then wash the powder with distilled water to a solution The pH value is about 8, and finally washed once with alcohol; the cleaned powder is dried in a vacuum environment, and the oxygen content of the dried powder is about 2500ppm; after drying, prevent contact with air and place it directly in a glove box with an argon atmosphere ;Powder doped with 40wt.% Nd 2 PR 1 Dy 1 Fe 14 The B alloy powder is rotated in a rolling ball mill for 1.5h, oriented and pressed in a...
PUM
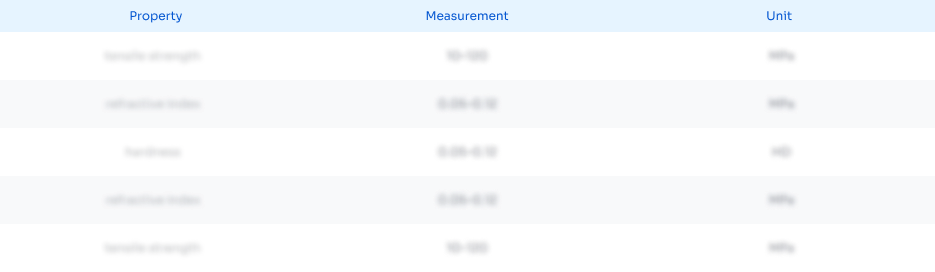
Abstract
Description
Claims
Application Information

- Generate Ideas
- Intellectual Property
- Life Sciences
- Materials
- Tech Scout
- Unparalleled Data Quality
- Higher Quality Content
- 60% Fewer Hallucinations
Browse by: Latest US Patents, China's latest patents, Technical Efficacy Thesaurus, Application Domain, Technology Topic, Popular Technical Reports.
© 2025 PatSnap. All rights reserved.Legal|Privacy policy|Modern Slavery Act Transparency Statement|Sitemap|About US| Contact US: help@patsnap.com