Preparation process of vanadium-nitrogen alloy
A preparation process and a technology for vanadium-nitrogen alloys are applied in the production field of vanadium-containing alloys, which can solve the problems of high production cost and poor quality, and achieve the effects of uniform product quality, good quality and guaranteed operation.
- Summary
- Abstract
- Description
- Claims
- Application Information
AI Technical Summary
Problems solved by technology
Method used
Examples
preparation example Construction
[0018] A preparation process for a vanadium-nitrogen alloy, comprising the following steps in turn:
[0019] The first step: First, the vanadium-containing compound is mechanically activated by grinding. The grinding time is greater than or equal to 1 hour, and then the reaction accelerator, graphene and binder are added for mixing to obtain a qualified mixture;
[0020] The second step: first place the above mixture for 24 hours, then mechanically shape the placed mixture into a coarse material block, and then perform aging treatment on the coarse material block, that is, the coarse material block is naturally dried at room temperature, and the processing time is longer than equal to 48 hours;
[0021] The third step: send the aging-treated coarse material into the calciner from the feed port of the vanadium-nitrogen alloy calciner, and at the same time, send high-purity nitrogen into the calciner through different inlets, and the coarse material After successively passing t...
Embodiment 1
[0028] The powdered vanadium pentoxide with a mass of 1000kg and a vanadium pentoxide grade of 98% is mechanically activated by grinding, and the grinding time is greater than or equal to 1 hour. After grinding, all of them pass through -180 mesh, and then add 10kg of ferrous carbonate Accelerator, adding 313.5kg of graphene with a fixed carbon content of 98% is a carbonizing agent, after dry mixing, add 70.5kg of water as a binder and wet mix evenly to obtain the mixture, after placing it for 24 hours, mechanically form it into a coarse Φ50 mm The block and coarse block are dried naturally for 48 hours and sent to the calcination kiln for calcination. The temperature in the drying stage is 400°C, the temperature in the carbonization stage is 1600°C, the temperature in the nitriding stage is 1350°C, and the cooling stage is water-cooled to The temperature does not exceed 100°C, the calcination time is 6 hours, the pressure in the kiln is slightly positive pressure, and the pres...
Embodiment 2
[0030] The vanadium trioxide with a quality of 1000kg and a metal vanadium content of 64.5% is mechanically activated by grinding. The grinding time is greater than or equal to 1 hour. purpose, vanadium pentoxide grade 98%) is a reaction accelerator, adding 278kg of graphene with a fixed carbon content of 98% is a carbonizing agent, after dry mixing evenly, add 112kg water and wet mix evenly to obtain a mixture, place it mechanically after 24 hours It is a coarse material block of Φ50 mm. The coarse material block is dried naturally for 48 hours and sent to a calcining kiln for calcination. The temperature in the drying stage is 300°C, the temperature in the carbonization stage is 1500°C, and the temperature in the nitriding stage is 1250°C. The cooling stage is water cooling to no more than 100°C, the calcination time is 6 hours, and the pressure in the kiln is slightly positive pressure, and the pressure range is 0.1kg / cm 3 , cooling out of the furnace will result in good su...
PUM
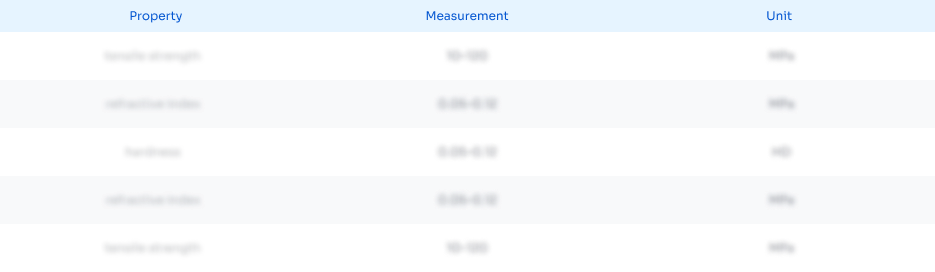
Abstract
Description
Claims
Application Information

- R&D
- Intellectual Property
- Life Sciences
- Materials
- Tech Scout
- Unparalleled Data Quality
- Higher Quality Content
- 60% Fewer Hallucinations
Browse by: Latest US Patents, China's latest patents, Technical Efficacy Thesaurus, Application Domain, Technology Topic, Popular Technical Reports.
© 2025 PatSnap. All rights reserved.Legal|Privacy policy|Modern Slavery Act Transparency Statement|Sitemap|About US| Contact US: help@patsnap.com