3D printing method and equipment
A 3D printing and printing-oriented technology, applied in the field of 3D printing, can solve the problems of long time-consuming printing and time-consuming growth.
- Summary
- Abstract
- Description
- Claims
- Application Information
AI Technical Summary
Problems solved by technology
Method used
Image
Examples
Embodiment 1
[0028] figure 1 It is a schematic flow chart of a 3D printing method provided in Embodiment 1 of the present invention. Such as figure 1 As shown, the 3D printing method provided in this embodiment specifically includes the following steps:
[0029] S101. Acquire height groups of the object to be printed in multiple different postures relative to the support platform, wherein the different height groups include heights of the object to be printed in at least one direction corresponding to different postures.
[0030] Wherein, the object to be printed can have a regular or irregular shape. In the traditional 3D printing process, the placement posture of the object to be printed is generally determined according to the distribution of its center of gravity, such as vertical or flat placement. However, in this embodiment, multiple possible postures of the object to be printed on the support platform need to be obtained, that is, multiple different orientations that the object t...
Embodiment 2
[0040] After obtaining multiple height groups of the object to be printed, when obtaining the first height, the second height, and the third height in the height group, you can set priorities for different heights, and obtain the first height in order according to the priority , the second height and the third height. figure 2 It is a schematic flowchart of obtaining the first height, the second height and the third height in multiple height groups of the object to be printed provided by the second embodiment of the present invention. Such as figure 2 As shown, specifically, in step S102, specifically, the following sub-steps may be included:
[0041] S1021. Obtain the first height with the smallest height among all height groups.
[0042] Specifically, the first height is the smallest height among all height groups, so its direction can match the direction with the slowest printing speed when printing the object to be printed, so as to save the consumption of printing tim...
Embodiment 3
[0053] On the basis of the second embodiment above, when obtaining multiple height groups of the object to be printed, and obtaining the first height, the second height and the third height from these height groups, the model of the object to be printed can be Grid division is performed on the grid, and the directions of the first height, the second height and the third height are determined according to the direction of each grid unit. image 3 It is a schematic flow chart of acquiring height groups of objects to be printed provided by Embodiment 3 of the present invention. Such as image 3 As shown, the steps of obtaining the height group of the object to be printed in multiple different postures relative to the support platform include:
[0054] S201. Obtain all polygonal faces composing the object to be printed.
[0055] Wherein, the model of the object to be printed can be composed of multiple polygonal surfaces, and the area size and quantity of the polygonal surfaces ...
PUM
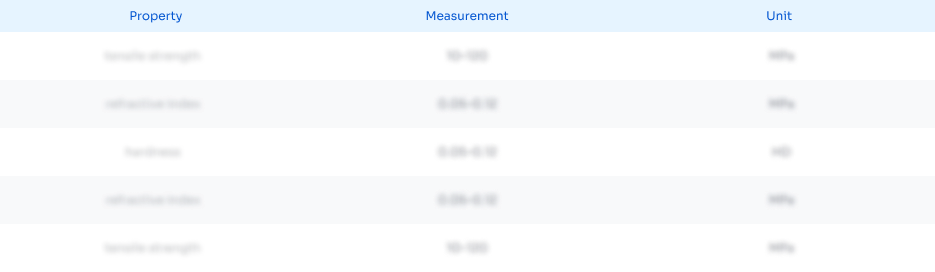
Abstract
Description
Claims
Application Information

- R&D
- Intellectual Property
- Life Sciences
- Materials
- Tech Scout
- Unparalleled Data Quality
- Higher Quality Content
- 60% Fewer Hallucinations
Browse by: Latest US Patents, China's latest patents, Technical Efficacy Thesaurus, Application Domain, Technology Topic, Popular Technical Reports.
© 2025 PatSnap. All rights reserved.Legal|Privacy policy|Modern Slavery Act Transparency Statement|Sitemap|About US| Contact US: help@patsnap.com