A kind of preparation method of lithium cobalt phosphate cathode material for lithium battery
A technology of lithium cobalt phosphate and cathode material, applied in battery electrodes, secondary batteries, circuits, etc., can solve the problems of low specific capacity, poor electrochemical performance stability, and low product stability of lithium cobalt phosphate cathode materials, and achieve enhanced The effect of electrochemical performance, enhanced coating, and improved electrochemical cycle performance
- Summary
- Abstract
- Description
- Claims
- Application Information
AI Technical Summary
Problems solved by technology
Method used
Examples
Embodiment 1
[0022] A method for preparing a lithium cobalt phosphate cathode material for a lithium battery, comprising the following steps:
[0023] (1) After mixing phosphoric acid and urea according to the mass ratio of 2:0.8, add water until completely dissolved, then raise the temperature to 80°C, and treat for 20 minutes;
[0024] (2) Mix ferrous chloride tetrahydrate powder and calcium acetate powder in an equal mass ratio, and the mixing process is carried out under air isolation conditions;
[0025] (3) Mix the material of step (1), the material of step (2) and lithium hydroxide at a vacuum degree of 0.02MPa according to a mass ratio of 1:1:3;
[0026] (4) Mix cobalt oxide and absolute ethanol solvent evenly at a mass ratio of 1:3, and add the mixture obtained in step (3) to it at a mass ratio of 1:1 at a stirring speed of 1000r / min, Stir evenly, heat and concentrate, and carry out sintering treatment in the presence of inert gas such as argon, the sintering temperature is 900°C...
Embodiment 2
[0028] A method for preparing a lithium cobalt phosphate cathode material for a lithium battery, comprising the following steps:
[0029] (1) After mixing phosphoric acid and urea according to the mass ratio of 2:1.3, add water until completely dissolved, then raise the temperature to 90°C, and treat for 30 minutes;
[0030] (2) Mix ferrous chloride tetrahydrate powder and calcium acetate powder in an equal mass ratio, and the mixing process is carried out under air isolation conditions;
[0031] (3) Mix the material of step (1), the material of step (2) and lithium hydroxide in a vacuum of 0.08 MPa, according to the mass ratio of 1:1:3;
[0032] (4) Mix cobalt oxide and absolute ethanol solvent uniformly at a mass ratio of 1:3, and add the mixture obtained in step (3) to it at a mass ratio of 1:1 at a stirring speed of 3000r / min, Stir evenly, heat and concentrate, and carry out sintering treatment in the presence of inert gas such as argon, the sintering temperature is 900-1...
Embodiment 3
[0034] A method for preparing a lithium cobalt phosphate cathode material for a lithium battery, comprising the following steps:
[0035] (1) After mixing phosphoric acid and urea at a mass ratio of 2:1, add water until completely dissolved, then raise the temperature to 85°C, and treat for 25 minutes;
[0036] (2) Mix ferrous chloride tetrahydrate powder and calcium acetate powder in an equal mass ratio, and the mixing process is carried out under air isolation conditions;
[0037] (3) Mix the material of step (1), the material of step (2) and lithium hydroxide at a vacuum degree of 0.06MPa according to a mass ratio of 1:1:3;
[0038] (4) Mix cobalt oxide and absolute ethanol solvent uniformly at a mass ratio of 1:3, and add the mixture obtained in step (3) to it at a mass ratio of 1:1 at a stirring speed of 2000r / min, Stir evenly, heat and concentrate, and sinter in the presence of argon and other inert gases. The sintering temperature is 1100°C, the sintering time is 9h, a...
PUM
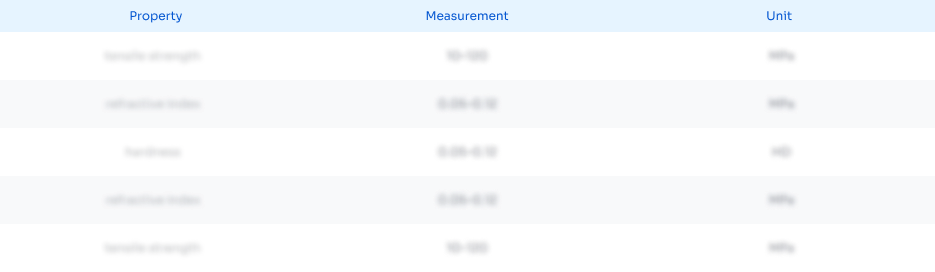
Abstract
Description
Claims
Application Information

- R&D
- Intellectual Property
- Life Sciences
- Materials
- Tech Scout
- Unparalleled Data Quality
- Higher Quality Content
- 60% Fewer Hallucinations
Browse by: Latest US Patents, China's latest patents, Technical Efficacy Thesaurus, Application Domain, Technology Topic, Popular Technical Reports.
© 2025 PatSnap. All rights reserved.Legal|Privacy policy|Modern Slavery Act Transparency Statement|Sitemap|About US| Contact US: help@patsnap.com