Design method of rubber forming mold of variable cross-section high-curvature differential flow adjusting cover part
A design method and technology for forming molds, applied in the field of sheet metal rubber forming, can solve the problems of inapplicability for mass production, poor surface quality of parts, and easy wrinkling of parts, and achieve simple structure, high tire reliability and smooth surface. Effect
- Summary
- Abstract
- Description
- Claims
- Application Information
AI Technical Summary
Problems solved by technology
Method used
Image
Examples
Embodiment 1
[0046] The front slide rail fairing parts of a new type of helicopter are made of 2A12 aluminum alloy material with a thickness of 0.8mm, see Figure 5 .
[0047] Design the shape and size of the punch according to the inner shape of the part. The end of the front slide rail fairing part has a large compression deformation. In order to avoid wrinkles, a bulging process allowance of 100mm is added; the end of the other side is stretched and deformed. To extend the allowance of 80mm, see Figure 6 .
[0048] 1) The concave mold is manufactured according to the size of the convex mold. The mold gap is taken on the concave mold, and the material thickness is 0.8mm for the gap. The compression deformation of one side of the middle area of the front slide fairing part is relatively large, and a draw bead is added to the extension area of the die, see Figure 7 .
[0049] 2) The upper surface of the die is consistent with the deformation of the part, and the lower surface is...
Embodiment 2
[0054] The lower saddle part of the air intake of a new helicopter is made of 6A02 aluminum alloy with a thickness of 1.2mm. See Figure 12 .
[0055] 1) Design the shape and size of the punch according to the inner shape of the part. The compression deformation of the two ends of the part is relatively large, and the bulging process allowance of 80mm is increased according to the shape. See Figure 13 .
[0056] 2) The concave mold is manufactured according to the cooperation of the convex mold, the mold gap is taken on the concave mold, and the material thickness of the gap is 1.2mm. The upper and lower surfaces of the die are flat, see Figure 14 .
[0057] 3) The inner shape of the pressing plate is manufactured according to the cooperation of the punch, the gap is taken on the pressing plate, and the material thickness is 1.2mm for the gap. The pressure plate and the lower surface are flat, see Figure 15 .
[0058] 4) For the rubber forming die structure of the low...
PUM
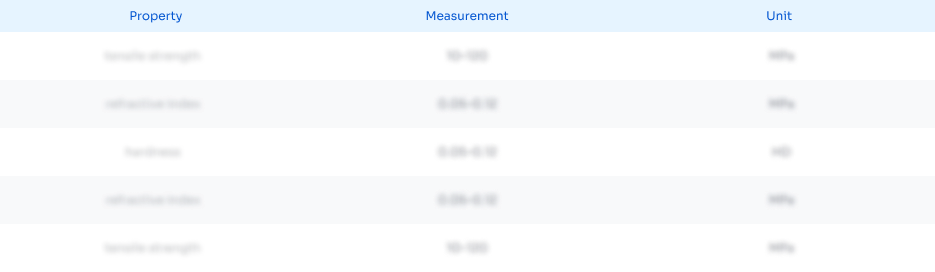
Abstract
Description
Claims
Application Information

- R&D
- Intellectual Property
- Life Sciences
- Materials
- Tech Scout
- Unparalleled Data Quality
- Higher Quality Content
- 60% Fewer Hallucinations
Browse by: Latest US Patents, China's latest patents, Technical Efficacy Thesaurus, Application Domain, Technology Topic, Popular Technical Reports.
© 2025 PatSnap. All rights reserved.Legal|Privacy policy|Modern Slavery Act Transparency Statement|Sitemap|About US| Contact US: help@patsnap.com