Flared flange pipe connecting system
A connection system and flanged pipe technology, applied in the field of flaring flange pipeline connection system, can solve problems such as long construction period, complicated welding process, pipeline leakage, etc., to reduce maintenance costs, ensure normal operation, and pass rate high effect
- Summary
- Abstract
- Description
- Claims
- Application Information
AI Technical Summary
Problems solved by technology
Method used
Image
Examples
Embodiment Construction
[0029] Such as figure 2 As shown, a flaring flange pipeline connection system includes a first branch pipe 1 and a second branch pipe 2, and the ends of the first branch pipe 1 and the second branch pipe 2 are respectively provided with tapered flares 3 , the first branch pipe 1 and the second branch pipe 2 are connected through a connection mechanism. The connection mechanism includes a first flange 4, a second flange 5, a first sealing cone 8, and a second sealing cone 9, and the first sealing cone 8 and the second sealing cone 9 both include a conical section and a cylindrical section, The conical section of the first sealing cone 8 is close to the inner end face of the tapered flare 3 of the first branch pipe 1, and the cylindrical section of the first sealing cone 8 stretches out from the tapered flare 3 of the first sealing cone 8; The conical section of the second sealing cone 9 is in close contact with the inner end surface of the tapered flare 3 of the second branch...
PUM
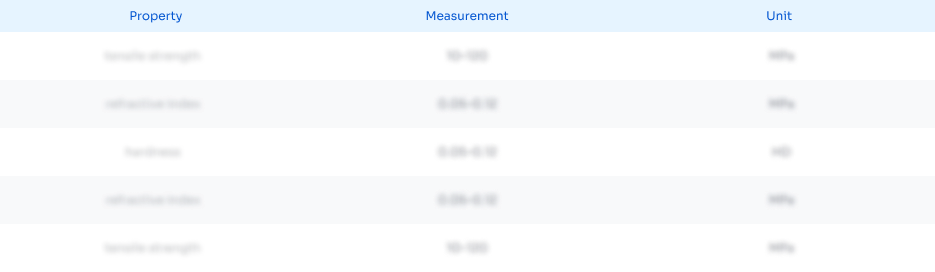
Abstract
Description
Claims
Application Information

- R&D
- Intellectual Property
- Life Sciences
- Materials
- Tech Scout
- Unparalleled Data Quality
- Higher Quality Content
- 60% Fewer Hallucinations
Browse by: Latest US Patents, China's latest patents, Technical Efficacy Thesaurus, Application Domain, Technology Topic, Popular Technical Reports.
© 2025 PatSnap. All rights reserved.Legal|Privacy policy|Modern Slavery Act Transparency Statement|Sitemap|About US| Contact US: help@patsnap.com