Solder resist process method for improving solder resist ghost
A process method and solder mask technology, applied in the secondary processing of printed circuits, electrical components, printed circuit manufacturing, etc., to save production costs, reduce production cycles, and improve the effect of blocking point nets
- Summary
- Abstract
- Description
- Claims
- Application Information
AI Technical Summary
Problems solved by technology
Method used
Image
Examples
Embodiment Construction
[0019] The specific embodiment of the present invention will be further described in detail below in conjunction with the accompanying drawings.
[0020] It should be noted that, in the following specific embodiments, when describing the embodiments of the present invention in detail, in order to clearly show the structure of the present invention for the convenience of description, the structures in the drawings are not drawn according to the general scale, and are drawn Partial magnification, deformation and simplification are included, therefore, it should be avoided to be interpreted as a limitation of the present invention.
[0021] In the following specific embodiments of the present invention, please refer to figure 1 . As shown in the figure, the present invention discloses a solder resist process method for improving solder resist ghosting, which is characterized in that it includes the following steps:
[0022] Step S1: Production of the blocking point net, adding ...
PUM
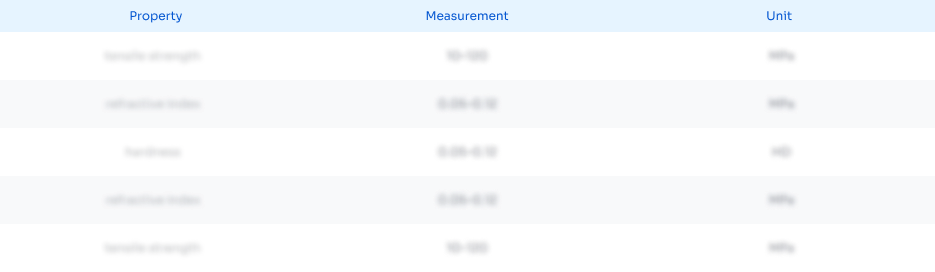
Abstract
Description
Claims
Application Information

- R&D
- Intellectual Property
- Life Sciences
- Materials
- Tech Scout
- Unparalleled Data Quality
- Higher Quality Content
- 60% Fewer Hallucinations
Browse by: Latest US Patents, China's latest patents, Technical Efficacy Thesaurus, Application Domain, Technology Topic, Popular Technical Reports.
© 2025 PatSnap. All rights reserved.Legal|Privacy policy|Modern Slavery Act Transparency Statement|Sitemap|About US| Contact US: help@patsnap.com