Contact network lead-wire wear measurement method and device based on multi-channel cameras
A measurement method and catenary technology, applied in the direction of measuring devices, optical devices, instruments, etc., can solve the problems of rigid suspension busbars without elasticity, large contact line wear, and large impulse, so that the wear situation can be monitored more intuitively, Easy to expand, convenient for timely feedback on the effect of maintenance and replacement
- Summary
- Abstract
- Description
- Claims
- Application Information
AI Technical Summary
Problems solved by technology
Method used
Image
Examples
Embodiment 1
[0059] Embodiment 1: A method for measuring the wear of catenary wires based on multi-channel cameras includes:
[0060] Step 1 (image acquisition step): n road cameras correspondingly collect n pieces of catenary wire images including the bottom of the catenary wire located in different pull-out value ranges;
[0061] Among them, the number of image acquisition cameras n is determined according to the range of the pull-out value of the contact line; the principle of determining the number of cameras is that n*D is greater than or equal to the maximum pull-out value range of the line contact line; where D is the maximum visible pull-out value range of a single camera ; The n-way cameras are installed on the roof of the detection train in parallel and perpendicular to the direction of the catenary wire. The installation method is as follows: Figure 4 Expand as shown. Where n is greater than or equal to 2, the n image acquisition cameras are distributed along a straight line pe...
PUM
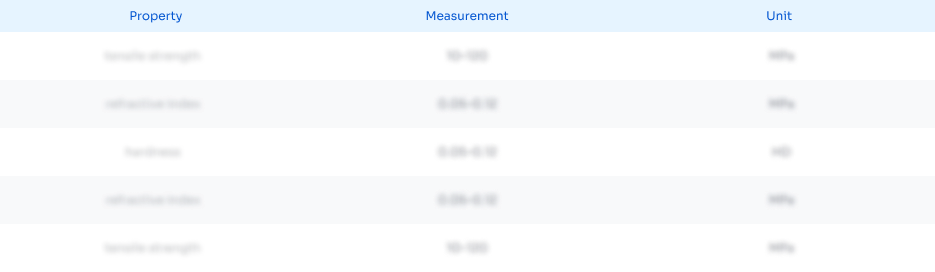
Abstract
Description
Claims
Application Information

- R&D
- Intellectual Property
- Life Sciences
- Materials
- Tech Scout
- Unparalleled Data Quality
- Higher Quality Content
- 60% Fewer Hallucinations
Browse by: Latest US Patents, China's latest patents, Technical Efficacy Thesaurus, Application Domain, Technology Topic, Popular Technical Reports.
© 2025 PatSnap. All rights reserved.Legal|Privacy policy|Modern Slavery Act Transparency Statement|Sitemap|About US| Contact US: help@patsnap.com