Acrylic emulsion specially used for stone-like coating as well as preparation method and application of acrylic emulsion
A technology of acrylic emulsion and real stone paint, applied in the direction of coating, etc., can solve the problems of increasing volatile organic compounds, slow drying speed of paint film, reducing hardness, etc., and achieves excellent performance
- Summary
- Abstract
- Description
- Claims
- Application Information
AI Technical Summary
Problems solved by technology
Method used
Image
Examples
preparation example Construction
[0039] The present invention also provides the preparation method of the acrylic acid emulsion described in the above technical scheme, comprising the following steps:
[0040] (1) mixing reactive emulsifier, acrylic acid, acrylamide, butyl acrylate, methyl methacrylate, special acrylate monomer and water to obtain a pre-emulsion;
[0041] (2) mixing acrylic acid, methyl methacrylate, room temperature self-crosslinking monomer and silane coupling agent to obtain shell monomer;
[0042] (3) mixing the reactive emulsifier, water and persulfate to obtain a reactive bottom material;
[0043] (4) adding the pre-emulsion and persulfate obtained in the step (1) dropwise to the reaction bottom material obtained in the step (3) to carry out free radical copolymerization, to obtain a nuclear emulsion;
[0044] (5) adding the shell monomer of the step (2) dropwise into the core emulsion of the step (4) to carry out the shell reaction, and then adding a pH regulator after the reaction to...
Embodiment 1
[0060] (1) Emulsification tank: according to the ratio in Table 1, put reactive emulsifier, acrylic acid, acrylamide, butyl acrylate, methyl methacrylate, special acrylate monomer and deionized water in the emulsification tank, Stir for 20 minutes to obtain a pre-emulsion;
[0061] (2) Head tank: place acrylic acid, methyl methacrylate, room temperature self-crosslinking monomer and silane coupling agent in the head tank, and stir for 20 minutes to obtain the shell monomer;
[0062] (3) Reactor: take the remaining weight of reactive emulsifier and deionized water, after heating to a temperature of 88°C, add 1 / 5 weight of potassium persulfate aqueous solution to obtain the reaction bottom material;
[0063] (4) Adding the emulsification tank pre-emulsion and 0.8 weight of potassium persulfate aqueous solution dropwise to the mixed solution at 87-88° C. for 3.0 hours, and nucleation reaction occurs for 1.0 hours of incubation to obtain a nuclear emulsion;
[0064] (5) Lower the...
Embodiment 2
[0067] Acrylic emulsion was prepared according to the ratio in Table 1 and the preparation method of Example 1, and the solid content of the acrylic emulsion prepared in Example 2 was 46%.
[0068] Raw material and consumption used in table 1 embodiment 1~4
[0069]
PUM
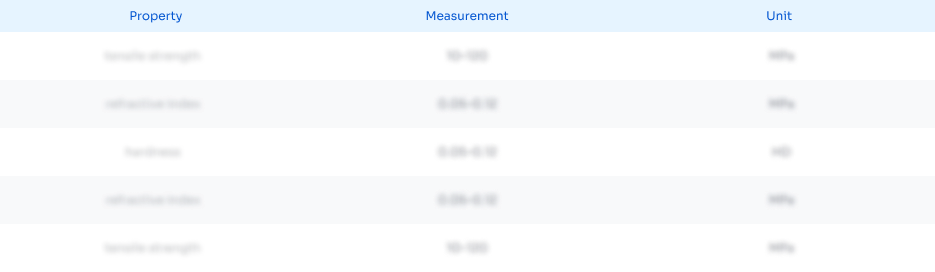
Abstract
Description
Claims
Application Information

- R&D
- Intellectual Property
- Life Sciences
- Materials
- Tech Scout
- Unparalleled Data Quality
- Higher Quality Content
- 60% Fewer Hallucinations
Browse by: Latest US Patents, China's latest patents, Technical Efficacy Thesaurus, Application Domain, Technology Topic, Popular Technical Reports.
© 2025 PatSnap. All rights reserved.Legal|Privacy policy|Modern Slavery Act Transparency Statement|Sitemap|About US| Contact US: help@patsnap.com