A kind of preparation method of temperature-responsive comb structure polycarboxylic acid
A temperature-responsive, comb-like structure technology, applied in the specific preparation field of comb-like structure polycarboxylic acid materials, to achieve excellent hydrophilic-hydrophobic conversion characteristics, increase contact angle, and inhibit shrinkage cracking
- Summary
- Abstract
- Description
- Claims
- Application Information
AI Technical Summary
Problems solved by technology
Method used
Image
Examples
Embodiment 1
[0035] First, 30g of tetrahydrofuran, 30g of methyl acrylate and 12.54g of isopropanol were added to the reactor, stirred and heated to 50°C, and then a mixed solution of 2.86g of azobisisobutyronitrile and 2.86g of tetrahydrofuran was added dropwise for 12 hours. After the addition, continue to react at a constant temperature of 50°C for 6 hours to obtain a self-polymerized product polymethyl acrylate solution; adjust the temperature of the obtained self-polymerized product to 50°C, add 35.22g of n-dodecyl mercaptan and stir for 40 minutes until it is mixed Evenly, add dropwise a mixed solution of 393.80g N-isopropylacrylamide, 28.57g azobisisobutyronitrile and 28.57g tetrahydrofuran for 12 hours, continue to react at a constant temperature of 50°C for 6 hours after the dropwise addition, and then distill under reduced pressure to remove Tetrahydrofuran to obtain graft copolymerization product; mix 423.80g graft copolymerization product with 62.64g deionized water, stir and he...
Embodiment 2
[0037] First, 210g of sulfolane, 30g of butyl acrylate and 6.47g of 3-mercaptopropanol were added to the reactor, stirred and heated to 110°C, and then a mixed solution of 2.53g of tert-butyl hydroperoxide and 10.13g of sulfolane was added dropwise for 3 hours. After the dropwise addition, continue to react at a constant temperature of 110°C for 2 hours to obtain a self-polymerized product polybutylacrylate solution; adjust the temperature of the obtained self-polymerized product to 90°C, add 24.85g of 3-mercaptopropionic acid and stir for 20 minutes until it is evenly mixed. Add a mixed solution of 148.86g N-tert-butylacrylamide, 12.66g tert-butyl hydroperoxide and 50.63g sulfolane dropwise for 3 hours, continue to react at a constant temperature of 90°C for 2 hours after the dropwise addition, and then distill under reduced pressure to remove the sulfolane. Obtain graft copolymerization product; Mix 178.86g graft copolymerization product with 21.07g deionized water, stir and ...
Embodiment 3
[0039] First, 270g dimethyl sulfoxide, 30g amyl acrylate and 1.27g isopropanol were added to the reactor, stirred and heated to 70°C, then 6.56g tert-butyl peroxybenzoate and 59.02g dimethyl Mix the solution of sulfoxide for 8 hours, continue to react at a constant temperature of 70°C for 4 hours after the dropwise addition, and obtain a polyamyl acrylate solution of the self-polymerized product; adjust the temperature of the obtained self-polymerized product to 80°C, and add 32.03g of n-dodecyl Mercaptan and stirred for 25 minutes until it was mixed evenly, and then a mixed solution of 97.59g N,N'-methylene bisacrylamide, 19.67g tert-butyl peroxybenzoate and 177.04g dimethyl sulfoxide was added dropwise for 6 hours, After the dropwise addition, continue to react at a constant temperature of 80°C for 3 hours, then distill off dimethyl sulfoxide under reduced pressure to obtain a graft copolymerization product; mix 127.56 g of the graft copolymerization product with deionized wa...
PUM
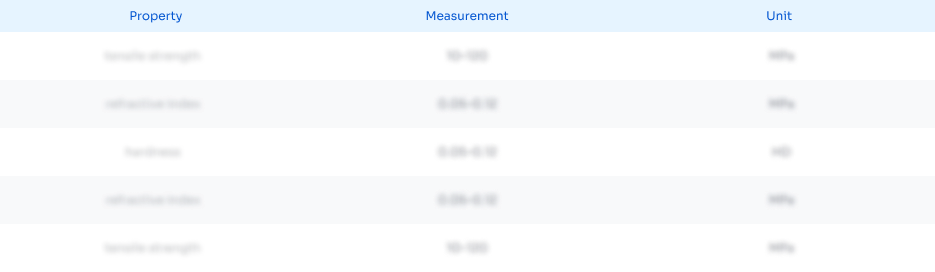
Abstract
Description
Claims
Application Information

- R&D
- Intellectual Property
- Life Sciences
- Materials
- Tech Scout
- Unparalleled Data Quality
- Higher Quality Content
- 60% Fewer Hallucinations
Browse by: Latest US Patents, China's latest patents, Technical Efficacy Thesaurus, Application Domain, Technology Topic, Popular Technical Reports.
© 2025 PatSnap. All rights reserved.Legal|Privacy policy|Modern Slavery Act Transparency Statement|Sitemap|About US| Contact US: help@patsnap.com