A thick film substrate miniaturized metal tube shell encapsulation structure
A packaging structure and metal tube technology, applied in the structural connection of printed circuits, printed circuits connected with non-printed electrical components, electrical components, etc., can solve the problems of inability to bond components and low circuit integration, and achieve The effect of reducing the difficulty of testing and simple assembly
- Summary
- Abstract
- Description
- Claims
- Application Information
AI Technical Summary
Problems solved by technology
Method used
Image
Examples
Embodiment Construction
[0028] The present invention will be further described below in conjunction with the accompanying drawings. The following examples are only used to illustrate the technical solution of the present invention more clearly, but not to limit the protection scope of the present invention.
[0029] combine figure 1 - Figure 4 In the present invention, the ceramic substrate and the printed board are mixed and assembled in the shell base, and the shell base 1 and the metal cap 2 are welded by laser to form a fully airtight package. Thick film and printed board miniaturized metal shell packaging design technology uses 2-layer PCB boards to be packaged on the pins of the shell base by soldering. The front and back of the lower PCB board 3 are completely surface-mounted, and the upper PCB board 4 Surface-mount parts are also used on the front and back, wherein a ceramic substrate 5 is welded to the front (upper surface) of the upper PCB board. The ceramic substrate 5 adopts a thick f...
PUM
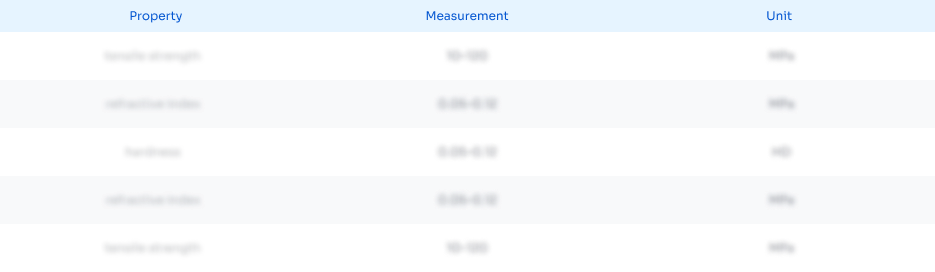
Abstract
Description
Claims
Application Information

- Generate Ideas
- Intellectual Property
- Life Sciences
- Materials
- Tech Scout
- Unparalleled Data Quality
- Higher Quality Content
- 60% Fewer Hallucinations
Browse by: Latest US Patents, China's latest patents, Technical Efficacy Thesaurus, Application Domain, Technology Topic, Popular Technical Reports.
© 2025 PatSnap. All rights reserved.Legal|Privacy policy|Modern Slavery Act Transparency Statement|Sitemap|About US| Contact US: help@patsnap.com