Preparation method of PBT porous fibers
A technology for porous fibers and raw materials, which is applied in the field of porous fibers, can solve the problems of complex, unusable, and limited drainage of alkali decomposition products, and achieve the effects of excellent hollow insulation performance, low cost, and improved performance.
- Summary
- Abstract
- Description
- Claims
- Application Information
AI Technical Summary
Problems solved by technology
Method used
Image
Examples
Embodiment 1
[0022] A method for preparing PBT porous fibers, first preparing spinning-grade PBT and spinning-grade PP, then drying the PBT raw materials to remove moisture in the raw materials; mixing PBT and PP uniformly according to the proportion and then melt-blending to prepare The blended gold is obtained; then the blended raw fiber is prepared by a twin-screw mixing extruder; the raw fiber is asymmetrically cooled, then cold-drawn, and the precursor is obtained after thermal relaxation; the obtained precursor is placed in a xylene solution Take it out after fully soaking in the medium, wash with ethanol, and dry to obtain PBT porous fiber.
[0023] The mass ratio of PBT and PP is 80:20. The PBT raw material was dried in a blast oven at 100° C. for 6 hours; the spinning temperature of the twin-screw extruder was 230° C., and the diameter of the spinneret was 1 mm.
[0024] Gained as-spun fibers after the melt spinning immediately enter the quenching chamber, and are cooled by the r...
Embodiment 2
[0029] A method for preparing PBT porous fibers, first preparing spinning-grade PBT and spinning-grade PP, then drying the PBT raw materials to remove moisture in the raw materials; mixing PBT and PP uniformly according to the proportion and then melt-blending to prepare The blended gold is obtained; then the blended raw fiber is prepared by a twin-screw mixing extruder; the raw fiber is asymmetrically cooled, then cold-drawn, and the precursor is obtained after thermal relaxation; the obtained precursor is placed in a xylene solution Take it out after fully soaking in the medium, wash with ethanol, and dry to obtain PBT porous fiber.
[0030] The mass ratio of PBT and PP is 60:40.
[0031] The PBT raw material was dried in a blast drying oven at 100° C. for 8 hours; the spinning temperature of the twin-screw extruder was 240° C., and the diameter of the spinneret was 2 mm.
[0032] Gained as-spun fiber immediately after the melt spinning enters the quenching chamber, and is ...
Embodiment 3
[0037]A method for preparing PBT porous fibers, first preparing spinning-grade PBT and spinning-grade PP, then drying the PBT raw materials to remove moisture in the raw materials; mixing PBT and PP uniformly according to the proportion and then melt-blending to prepare The blended gold is obtained; then the blended raw fiber is prepared by a twin-screw mixing extruder; the raw fiber is asymmetrically cooled, then cold-drawn, and the precursor is obtained after thermal relaxation; the obtained precursor is placed in a xylene solution Take it out after fully soaking in the medium, wash with ethanol, and dry to obtain PBT porous fiber.
[0038] The mass ratio of PBT and PP is 70:30.
[0039] The PBT raw material was dried in a blast oven at 100° C. for 7 hours; the spinning temperature of the twin-screw extruder was 235° C., and the diameter of the spinneret was 1 mm.
[0040] Gained as-spun fibers after the melt spinning immediately enter the quenching chamber, and are cooled ...
PUM
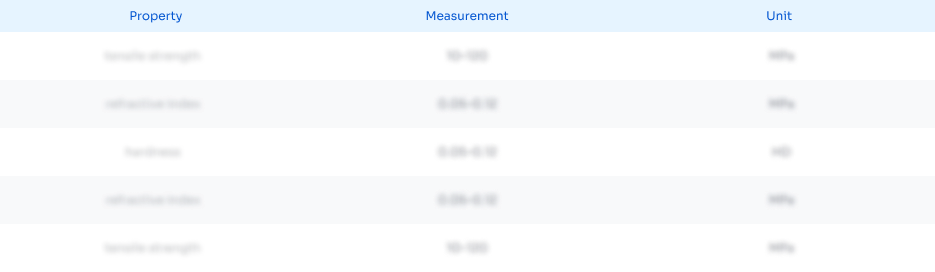
Abstract
Description
Claims
Application Information

- Generate Ideas
- Intellectual Property
- Life Sciences
- Materials
- Tech Scout
- Unparalleled Data Quality
- Higher Quality Content
- 60% Fewer Hallucinations
Browse by: Latest US Patents, China's latest patents, Technical Efficacy Thesaurus, Application Domain, Technology Topic, Popular Technical Reports.
© 2025 PatSnap. All rights reserved.Legal|Privacy policy|Modern Slavery Act Transparency Statement|Sitemap|About US| Contact US: help@patsnap.com