Rapid forming process of large flange of high-power wind power main shaft
A technology of wind power spindle and forming process, which is applied in manufacturing tools, metal processing equipment, forging/pressing/hammer devices, etc. Mechanical properties, improve the density of the tissue, increase the effect of the drawing ratio
- Summary
- Abstract
- Description
- Claims
- Application Information
AI Technical Summary
Problems solved by technology
Method used
Image
Examples
Embodiment 1
[0041] The forging technological process of the present invention is as image 3 shown, including steps:
[0042] (1) Casting steel ingot blanks, including octagonal material 101 with a large upper end and a small lower end and a riser 102 at the upper end, the octagonal material 101 has an octagonal cross section and a trapezoidal longitudinal section; then cut off the nozzle and cut off the riser flash;
[0043] (2) The first fire forging
[0044] 2a) The billet is put into the furnace and heated to 1170-1230°C, kept for 7-12 hours before being released from the furnace;
[0045] 2b) Press the riser 102 into a clamp handle 103, and upset the drain plate 11 (the clamp handle 103 is placed in the leak hole of the drain plate 11), and the height H of the square material 101 after upsetting is 0.4 to 0.6 times the original length , and then extended to 1.7-2.3H;
[0046] 2c) Then enter the leaking plate and upset to the height H, then pull it out, and cut out the material dis...
PUM
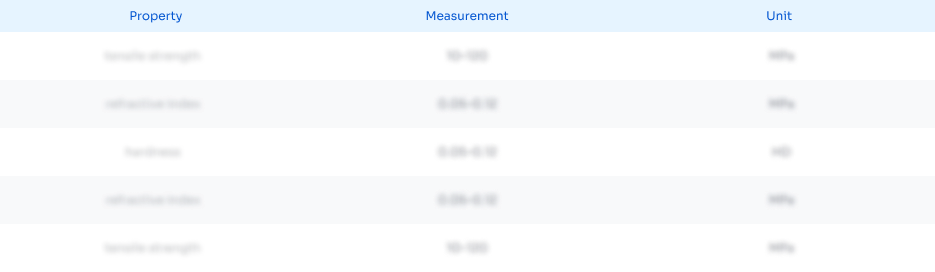
Abstract
Description
Claims
Application Information

- R&D
- Intellectual Property
- Life Sciences
- Materials
- Tech Scout
- Unparalleled Data Quality
- Higher Quality Content
- 60% Fewer Hallucinations
Browse by: Latest US Patents, China's latest patents, Technical Efficacy Thesaurus, Application Domain, Technology Topic, Popular Technical Reports.
© 2025 PatSnap. All rights reserved.Legal|Privacy policy|Modern Slavery Act Transparency Statement|Sitemap|About US| Contact US: help@patsnap.com