Compound forming method of flow spinning and double-roller clamping spinning
A technology of flow spinning and compound forming, which is applied in the field of compound forming of flow spinning and double-roller clamping spinning, to achieve obvious economic benefits, high forming accuracy and production efficiency, and avoid repeated clamping and positioning
- Summary
- Abstract
- Description
- Claims
- Application Information
AI Technical Summary
Problems solved by technology
Method used
Image
Examples
Embodiment Construction
[0022] The present invention will be further described in detail below in conjunction with the drawings.
[0023] Reference figure 1 with figure 2 , The equipment used in a composite forming method of flow spinning and double-roll clamping spinning, including internal expansion clamping device 1, flow spinning wheel 2, core mold 3 and double-roll clamping spinning Roller 4; the thick-walled seamless tube blank 5 used is wall thickness t 0 , Inner diameter R 0 , Length L 0 Seamless pipe; the product to be formed is wall thickness t 1 , Inner diameter R 0 , Straight length L 1 , Flange length l 1 Of thin-walled rotary body parts with complex flange curved surface; the core mold 3 used is the outer diameter R 0 , Length L 0 Cylindrical parts.
[0024] According to the flow spinning forming theory, the thin-walled rotating body parts with complex flange curved surfaces and thick-walled seamless tube blanks to be formed 5 satisfy:
[0025]
[0026] A composite forming method of flow spi...
PUM
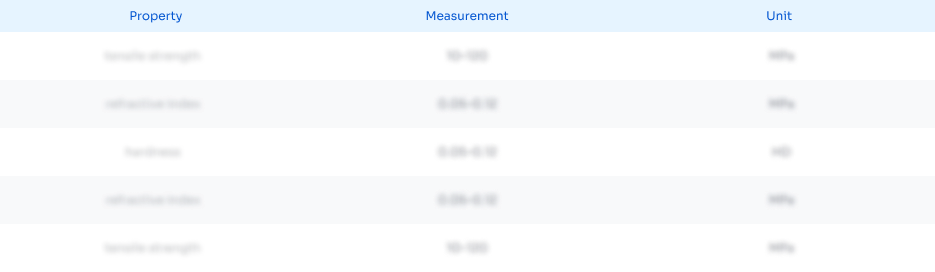
Abstract
Description
Claims
Application Information

- Generate Ideas
- Intellectual Property
- Life Sciences
- Materials
- Tech Scout
- Unparalleled Data Quality
- Higher Quality Content
- 60% Fewer Hallucinations
Browse by: Latest US Patents, China's latest patents, Technical Efficacy Thesaurus, Application Domain, Technology Topic, Popular Technical Reports.
© 2025 PatSnap. All rights reserved.Legal|Privacy policy|Modern Slavery Act Transparency Statement|Sitemap|About US| Contact US: help@patsnap.com