Molding element for manufacturing a noise reducing tread
A technology for molding components and treads, applied to tire parts, tire treads/tread patterns, tires, etc., can solve problems such as difficult to obtain treads with flexible fences, reduce processing duration, increase productivity, The effect of increasing degrees of freedom
- Summary
- Abstract
- Description
- Claims
- Application Information
AI Technical Summary
Problems solved by technology
Method used
Image
Examples
Embodiment Construction
[0053] Preferred embodiments of the present invention will be described below with reference to the accompanying drawings.
[0054] The following will refer to Figure 1 to Figure 7 A molding element 1 of a mold for manufacturing a tread 101 of a tire, a mold including the molding element 1 , and a tread 101 molded and vulcanized using the mold according to an embodiment of the present invention will be described.
[0055] figure 1 is a schematic plan view of a tread of a tire molded with a mold including a molding element according to an embodiment of the present invention. figure 2 is displayed figure 1 An enlarged schematic plan view of the portion indicated as II in . image 3 is along figure 1 A schematic cross-sectional view taken along line III-III in . Figure 4 is a schematic perspective view of a part of a molding element without an insert according to an embodiment of the invention. Figure 5 is a schematic perspective view of a part of a molding element wi...
PUM
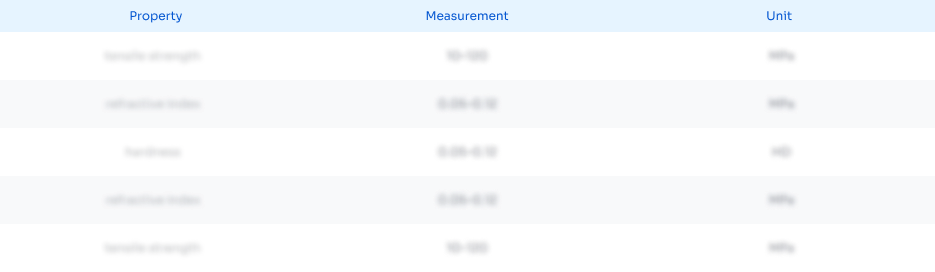
Abstract
Description
Claims
Application Information

- R&D Engineer
- R&D Manager
- IP Professional
- Industry Leading Data Capabilities
- Powerful AI technology
- Patent DNA Extraction
Browse by: Latest US Patents, China's latest patents, Technical Efficacy Thesaurus, Application Domain, Technology Topic, Popular Technical Reports.
© 2024 PatSnap. All rights reserved.Legal|Privacy policy|Modern Slavery Act Transparency Statement|Sitemap|About US| Contact US: help@patsnap.com