Fault diagnosis method for piston-type air compressor crankcase rolling bearing
A rolling bearing and fault diagnosis technology, which is applied in the testing of mechanical components, testing of machine/structural components, measuring devices, etc., can solve fault missed detection, periodic impact characteristic interference, and difficult to solve piston air compressor fault bearing diagnosis Problems and other problems, to achieve the effect of fast and accurate identification
- Summary
- Abstract
- Description
- Claims
- Application Information
AI Technical Summary
Problems solved by technology
Method used
Image
Examples
Embodiment Construction
[0041] In order to make the object, technical solution and advantages of the present invention clearer, the present invention will be further described in detail below in conjunction with the accompanying drawings.
[0042] The specific steps of a fault diagnosis method for crankcase rolling bearings of piston air compressors are as follows:
[0043] First, the rolling bearing vibration signal collected from the piston air compressor is used as the original signal for VMD processing to obtain a series of modal components containing fault information. The detailed steps of VMD processing are as follows:
[0044] VMD technology can decompose the non-stationary signal y(t) into a group of modal components located near the center frequency, and the signal y(t) can be expressed as the following formula:
[0045] y(t)=∑ k u k (1)
[0046] The essence of VMD is to solve the optimal solution of the constrained variational model, which is given by the following formula:
[0047] ...
PUM
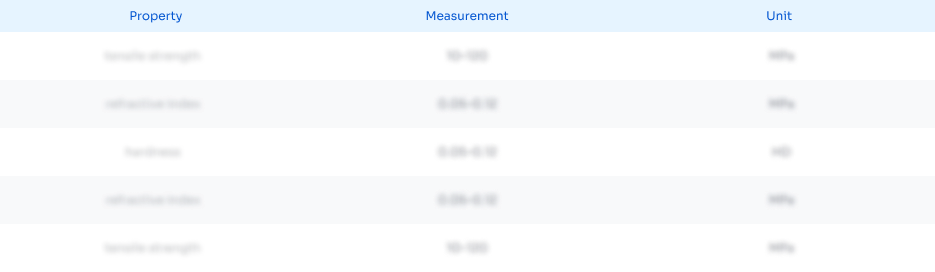
Abstract
Description
Claims
Application Information

- R&D
- Intellectual Property
- Life Sciences
- Materials
- Tech Scout
- Unparalleled Data Quality
- Higher Quality Content
- 60% Fewer Hallucinations
Browse by: Latest US Patents, China's latest patents, Technical Efficacy Thesaurus, Application Domain, Technology Topic, Popular Technical Reports.
© 2025 PatSnap. All rights reserved.Legal|Privacy policy|Modern Slavery Act Transparency Statement|Sitemap|About US| Contact US: help@patsnap.com