Powder metallurgy brake pad and preparing method thereof
A technology of powder metallurgy and brake pads, which is applied in the field of powder metallurgy brake pads and its preparation, can solve problems such as the failure to meet the requirements of wading recovery performance, high-temperature thermal degradation of brake pads, and insufficient static parking torque on slopes, etc., to achieve superior performance, Accelerate wear and improve the effect of high temperature heat decay
- Summary
- Abstract
- Description
- Claims
- Application Information
AI Technical Summary
Problems solved by technology
Method used
Image
Examples
Embodiment 1
[0029] Friction material composition: see Table 1.
[0030] The raw material particle size of the friction material is: iron powder-200 mesh, copper powder-200 mesh, molybdenum trioxide-325 mesh, graphite-40 mesh, silicon oxide-325 mesh, aluminum oxide-325 mesh, nickel powder-400 mesh.
[0031] Preparation:
[0032] (1) Carry out degreasing and copper-plating pretreatment on the steel back connected with the friction material of the brake pad, and wait for use after the treatment is completed;
[0033] (2) Put the weighed raw materials into the mixer, the rotating speed of the mixer is 25r / min, and the mixing time is 60 minutes.
[0034] (3) Add the mixed powder into the mold cavity and press it, the pressing pressure is 300MPa, and the holding time is 20s;
[0035] (4) Put the pressed green compact and the pretreated steel back into a sintering furnace for sintering, the sintering temperature is 1050° C., and the holding time is 120 minutes.
[0036] (5) After the steel ba...
Embodiment 2
[0041] Friction material composition: see Table 1.
[0042] The raw material particle size of the friction material is: iron powder-200 mesh, copper powder-200 mesh, molybdenum trioxide-325 mesh, graphite-40 mesh, silicon oxide-325 mesh, aluminum oxide-325 mesh, nickel powder-400 mesh.
[0043] Preparation:
[0044] (1) Carry out degreasing and copper-plating pretreatment on the steel back connected with the friction material of the brake pad, and wait for use after the treatment is completed;
[0045] (2) Put the weighed raw materials into the mixer, the rotating speed of the mixer is 25r / min, and the mixing time is 70 minutes.
[0046] (3) Add the mixed powder into the mold cavity and press it with a pressing pressure of 250MPa and a holding time of 15s;
[0047] (4) Put the pressed compact and the pretreated steel back into a sintering furnace for sintering, the sintering temperature is 1000° C., and the holding time is 90 minutes.
[0048] (5) After the steel back and t...
Embodiment 3
[0053] Friction material composition: see Table 1.
[0054] The raw material particle size of the friction material is: iron powder-200 mesh, copper powder-200 mesh, molybdenum trioxide-325 mesh, graphite-40 mesh, silicon oxide-325 mesh, aluminum oxide-325 mesh, nickel powder-400 mesh.
[0055] Preparation:
[0056] (1) Carry out degreasing and copper-plating pretreatment on the steel back connected with the friction material of the brake pad, and wait for use after the treatment is completed;
[0057] (2) Put the weighed raw materials into the mixer, the rotating speed of the mixer is 25r / min, and the mixing time is 70 minutes.
[0058] (3) Add the mixed powder into the mold cavity and press it, the pressing pressure is 200MPa, and the holding time is 30s;
[0059] (4) Put the pressed green compact and the pretreated steel back into a sintering furnace for sintering, the sintering temperature is 1050° C., and the holding time is 60 minutes.
[0060] (5) After the steel bac...
PUM
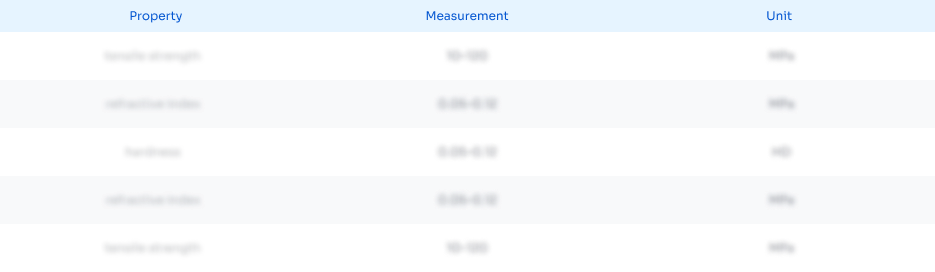
Abstract
Description
Claims
Application Information

- Generate Ideas
- Intellectual Property
- Life Sciences
- Materials
- Tech Scout
- Unparalleled Data Quality
- Higher Quality Content
- 60% Fewer Hallucinations
Browse by: Latest US Patents, China's latest patents, Technical Efficacy Thesaurus, Application Domain, Technology Topic, Popular Technical Reports.
© 2025 PatSnap. All rights reserved.Legal|Privacy policy|Modern Slavery Act Transparency Statement|Sitemap|About US| Contact US: help@patsnap.com