Method for repairing steel tapping face furnace lining through final slag of rotating furnace
A converter and final slag technology, applied in the manufacture of converters and other directions, can solve problems such as the length of sintering time, and achieve the effect of good repairing effect, low repairing cost and improving converter operation rate.
- Summary
- Abstract
- Description
- Claims
- Application Information
AI Technical Summary
Problems solved by technology
Method used
Image
Examples
Embodiment 1
[0025] The steel type for the repair furnace is Q235B: molten iron ω[Si]=0.40%, the amount of molten iron charged is 60.8t, when smelting and slagging, metallurgical lime and light burnt dolomite are added to the molten steel, of which the amount of metallurgical lime added is 1967kg, The amount of light-burned dolomite added is 1021kg; the end point of the converter controls molten steel [C]=0.109%, the tapping temperature is 1659°C, the basicity R of the final slag of the converter is 3.3, the percentage of MgO in the slag is 8.61%, and the percentage of FeO 14.56%; when pouring slag, the angle of slag pouring is 85°, and the amount of slag remaining is controlled to be 5t; after the molten steel is cleaned, the slag splashing treatment is carried out for 1.5min, the temperature of the slag is appropriately reduced, and the viscosity of the slag is increased, and then the furnace mouth of the converter faces the steel surface Inclined at 72°, spread the final slag of the conv...
Embodiment 2
[0027] The steel type of the repair furnace is HRB400B: molten iron ω[Si]=0.46%, the amount of molten iron charged is 60.3t, when smelting and slagging, metallurgical lime and light burnt dolomite are added to the molten steel, of which the amount of metallurgical lime added is 2296kg, The amount of light-burned dolomite added is 1528kg; the molten steel [C]=0.113% is controlled at the end point of the converter, the tapping temperature is 1655°C, the basicity R of the final slag of the converter is 3.2, the percentage of MgO in the slag is 8.52%, and the percentage of FeO 14.28%; when pouring slag, the angle of slag pouring is 86°, and the amount of slag remaining is controlled to be 5t; after the molten steel is cleaned, the slag splashing treatment is carried out for 1.6min, the temperature of the slag is appropriately reduced, and the viscosity of the slag is increased, and then the furnace mouth of the converter faces the steel surface Inclined at 73°, spread the final sla...
Embodiment 3
[0029] The steel type of the repair furnace is SS400B: molten iron ω[Si]=0.50%, the amount of molten iron charged is 60.5t, when smelting and slagging, metallurgical lime and light burnt dolomite are added to the molten steel, of which the amount of metallurgical lime added is 2512kg, The amount of light-burned dolomite added is 1672kg; the end point of the converter controls molten steel [C] = 0.091%, the tapping temperature is 1664°C, the basicity R of the final slag of the converter is 3.4, the percentage of MgO in the slag is 9.31%, and the percentage of FeO 13.47%; when pouring slag, the angle of slag pouring is 85°, and the amount of slag remaining is controlled to 4t; after the molten steel is cleaned, the slag splashing treatment is carried out for 1.2min, the temperature of the slag is appropriately lowered, and the viscosity of the slag is increased, and then the furnace mouth of the converter faces the steel surface Inclined at 74°, spread the final slag of the conve...
PUM
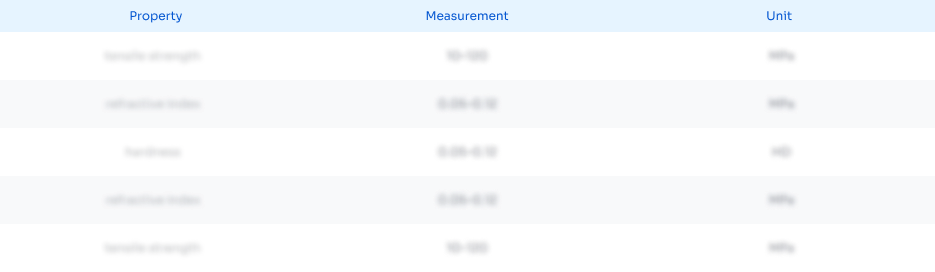
Abstract
Description
Claims
Application Information

- R&D
- Intellectual Property
- Life Sciences
- Materials
- Tech Scout
- Unparalleled Data Quality
- Higher Quality Content
- 60% Fewer Hallucinations
Browse by: Latest US Patents, China's latest patents, Technical Efficacy Thesaurus, Application Domain, Technology Topic, Popular Technical Reports.
© 2025 PatSnap. All rights reserved.Legal|Privacy policy|Modern Slavery Act Transparency Statement|Sitemap|About US| Contact US: help@patsnap.com