Low-oxygen refining slag system for smelting steel and preparation method and application of low-oxygen refining slag system
A technology for refining slag and molten steel, which is applied in the field of iron and steel smelting to achieve the effects of reducing the number of refurbishments, good fluidity, and avoiding the formation of oxide inclusions
- Summary
- Abstract
- Description
- Claims
- Application Information
AI Technical Summary
Problems solved by technology
Method used
Image
Examples
Embodiment 1
[0029] A low-oxygen refining slag system for steelmaking, the main components of which are as follows:
[0030] CaO 8%, SiO 2 3%, MgO 20%, Al 2 o 3 16%, CaF 2 53%.
[0031] A method for preparing a low-oxygen refining slag system for smelting steel, comprising the following steps:
[0032] Step 1, prepare the raw materials, dry the raw materials, weigh them according to the proportioning requirements, and mix them evenly;
[0033] Step 2, the uniformly mixed raw materials are melted in a melting furnace protected by an argon atmosphere, the melting temperature is controlled between 1600°C, and the melting time is 20 minutes;
[0034] Step 3: After the smelting is completed, the pre-melted slag system is taken out from the melting furnace and quenched with water, and the pre-melted slag system is mechanically crushed to obtain the refined slag system.
[0035] The refining slag after step three mechanical crushing is 16 mesh.
[0036] An application of a low-oxygen re...
Embodiment 2
[0039] A low-oxygen refining slag system for steelmaking, the main components of which are as follows:
[0040] CaO 12%, SiO 2 4%, MgO 17%, Al 2 o 3 13%, CaF 2 54%.
[0041] A method for preparing a low-oxygen refining slag system for smelting steel, comprising the following steps:
[0042] Step 1, prepare the raw materials, dry the raw materials, weigh them according to the proportioning requirements, and mix them evenly;
[0043] Step 2, the uniformly mixed raw materials are melted in a melting furnace protected by an argon atmosphere, the melting temperature is controlled between 1610°C, and the melting time is 18 minutes;
[0044] Step 3: After the smelting is completed, the pre-melted slag system is taken out from the melting furnace and quenched with water, and the pre-melted slag system is mechanically crushed to obtain the refined slag system.
[0045] The refining slag after step three mechanical crushing is 17 mesh.
[0046]In this example, the same deoxida...
Embodiment 3
[0048] A low-oxygen refining slag system for steelmaking, the main components of which are as follows:
[0049] CaO 14%, SiO 2 6%, MgO 17%, Al 2 o 3 8%, CaF 2 55%.
[0050] A method for preparing a low-oxygen refining slag system for smelting steel, comprising the following steps:
[0051] Step 1, prepare the raw materials, dry the raw materials, weigh them according to the proportioning requirements, and mix them evenly;
[0052] Step 2, the uniformly mixed raw materials are melted in a melting furnace protected by an argon atmosphere, the melting temperature is controlled between 1620°C, and the melting time is 15 minutes;
[0053] Step 3: After the smelting is completed, the pre-melted slag system is taken out from the melting furnace and quenched with water, and the pre-melted slag system is mechanically crushed to obtain the refined slag system.
[0054] The refining slag after step three mechanical crushing is 17 mesh.
[0055] In this example, the same deoxida...
PUM
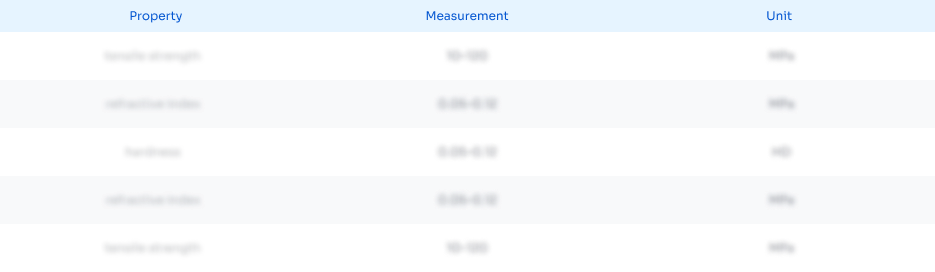
Abstract
Description
Claims
Application Information

- R&D Engineer
- R&D Manager
- IP Professional
- Industry Leading Data Capabilities
- Powerful AI technology
- Patent DNA Extraction
Browse by: Latest US Patents, China's latest patents, Technical Efficacy Thesaurus, Application Domain, Technology Topic, Popular Technical Reports.
© 2024 PatSnap. All rights reserved.Legal|Privacy policy|Modern Slavery Act Transparency Statement|Sitemap|About US| Contact US: help@patsnap.com