Processing method of surface-carbonized poplar solid wood floor
A processing method and carbonization technology, applied in the direction of wood processing utensils, wood treatment, manufacturing tools, etc., can solve the problems of aggravating the shortage of high-quality wood supply, unable to use solid wood floors, easy to deform, etc., to achieve the degree of carbonization and uniformity, easy to control, Maintain natural performance, save time
- Summary
- Abstract
- Description
- Claims
- Application Information
AI Technical Summary
Problems solved by technology
Method used
Image
Examples
Embodiment 1
[0021] A kind of processing method of surface carbonized poplar solid wood floor provided by the invention comprises the following steps:
[0022] S1. Surface densification treatment: Saw poplar wood into poplar boards with a thickness of 20mm, put them in a drying kiln and dry them to a moisture content of 10%, and then put them into a hot press for compression and densification treatment. The surface of the poplar board is sprayed and softened for 5 minutes, and kept for 15 minutes under hot pressing pressure of 1.1MPa and temperature of 180°C;
[0023] S2, cutting the poplar plank into floor blanks, the size of which is 920×127×16mm;
[0024] S3. Carbonization treatment of floor blank material: put the floor blank into a high-temperature carbonization tank, use steam or nitrogen as a protective gas, and carry out carbonization treatment. The carbonization temperature is 220°C and the time is 15 minutes; the carbonization treatment in step S3 is carried out in four stages. ...
Embodiment 2
[0027] S1. Surface densification treatment: Saw poplar wood into poplar boards with a thickness of 25mm, put them in a drying kiln and dry them to a moisture content of 12%, and then put them into a hot press for compression and densification treatment. The surface of the poplar board is sprayed and softened for 3 minutes, and kept for 20 minutes under hot pressing pressure of 1MPa and temperature of 160°C;
[0028] S2, cutting the poplar board into floor blanks, the size of which is 920×127×18mm;
[0029] S3. Carbonization treatment of floor blank material: put the floor blank into a high-temperature carbonization tank, use steam or nitrogen as a protective gas, and carry out carbonization treatment. The carbonization temperature is 280 ° C, and the time is 20 minutes; the carbonization treatment in step S3 is carried out in four stages. In the preheating stage, the carbonization furnace is first heated to 150°C for preheating. The second stage is the rapid heating stage: qui...
PUM
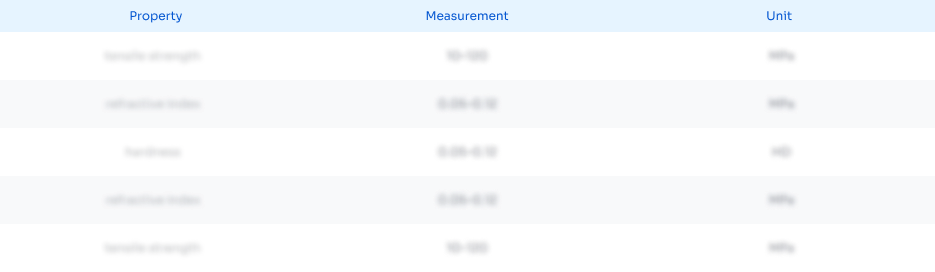
Abstract
Description
Claims
Application Information

- R&D
- Intellectual Property
- Life Sciences
- Materials
- Tech Scout
- Unparalleled Data Quality
- Higher Quality Content
- 60% Fewer Hallucinations
Browse by: Latest US Patents, China's latest patents, Technical Efficacy Thesaurus, Application Domain, Technology Topic, Popular Technical Reports.
© 2025 PatSnap. All rights reserved.Legal|Privacy policy|Modern Slavery Act Transparency Statement|Sitemap|About US| Contact US: help@patsnap.com