Quality control method and device for blade linear friction welding joint
A linear friction welding and control device technology, applied in welding equipment, manufacturing tools, non-electric welding equipment, etc., can solve problems such as waste of precious metals, welding defects, and reduce welding area, so as to achieve the effect of reducing waste and uniform heat production
- Summary
- Abstract
- Description
- Claims
- Application Information
AI Technical Summary
Problems solved by technology
Method used
Image
Examples
Embodiment 1
[0029] Such as figure 1 As shown, this embodiment proposes a method for quality control of blade linear friction welding joints, the method comprising:
[0030] S101. Intercepting the section of the blade at the height of the welding position, and offsetting the two sides of the position where the thickness of the section of the blade is the largest.
[0031] Specifically, in this embodiment, a certain welding allowance can be reserved by offsetting the two sides of the position where the thickness of the blade section is the largest. If you choose a position with a smaller thickness, it is easy to have no margin in other positions, resulting in poor welding. However, if the margin is too large, it will affect the frictional pressure of the welding process and also cause welding defects. Therefore, in this embodiment, the margin is set between 2 mm and 5 mm, that is, the distance between the two sides after the shift and the original position is 2 mm to 5 mm.
[0032] S102....
Embodiment 2
[0039] This embodiment proposes a quality control device for linear friction welding joints of blades, the device includes a processor, and the processor is embedded with operational instructions executable by the processor, and has performed the following operations:
[0040] Obtain the blade section at the height of the welding position;
[0041] offsetting the two sides of the position where the section thickness of the blade is the largest;
[0042] Draw a circle with the maximum distance between the two sides after the offset as the diameter, and the center of the circle is the midpoint of the maximum distance line segment between the two sides after the offset;
[0043] moving the center of the circle along the centerline of the blade section to form a contour track;
[0044] Connect the farthest points of all the circles in the contour trajectory on both sides of the blade section, and the area enclosed by the two line segments after the connection and the circles at b...
PUM
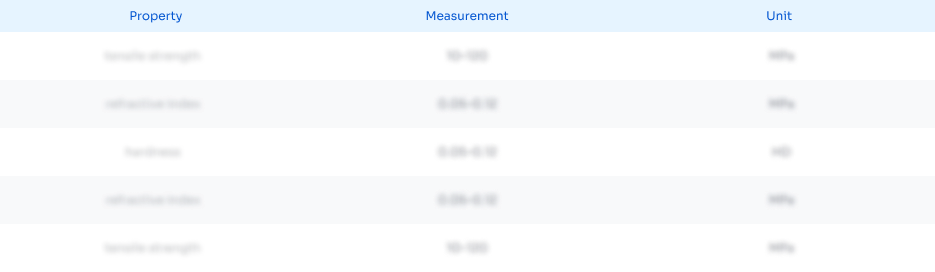
Abstract
Description
Claims
Application Information

- R&D
- Intellectual Property
- Life Sciences
- Materials
- Tech Scout
- Unparalleled Data Quality
- Higher Quality Content
- 60% Fewer Hallucinations
Browse by: Latest US Patents, China's latest patents, Technical Efficacy Thesaurus, Application Domain, Technology Topic, Popular Technical Reports.
© 2025 PatSnap. All rights reserved.Legal|Privacy policy|Modern Slavery Act Transparency Statement|Sitemap|About US| Contact US: help@patsnap.com