Novel mixed matrix membrane for gas separation, and preparation method thereof
A mixed matrix membrane and gas separation technology, which is applied in semipermeable membrane separation, chemical instruments and methods, membrane technology, etc., can solve the problems of high preparation cost and difficulty in processing, and achieve the purpose of increasing adsorption active centers, improving strength and durability properties, increasing the specific surface area
- Summary
- Abstract
- Description
- Claims
- Application Information
AI Technical Summary
Problems solved by technology
Method used
Examples
Embodiment 1
[0027] Example 1: Zeolite-AlN / SiO 2 Preparation of nanoparticles 1:
[0028] This implementation prepares zeolite-AlN / SiO 2 The steps for nanoparticles are as follows:
[0029] Zeolite modification: roast 100g of zeolite at 300°C for 60 minutes, take it out and cool it, then put it into 35wt% hydrochloric acid solution and heat it to reflux for 8 hours, take it out, wash it, dry it, and set it aside;
[0030] Aluminum powder activation: 120g of aluminum powder and zirconia are milled in argon atmosphere at low temperature and high energy for 30h at 5°C, the ball milling speed is 500rpm, the mass ratio of zirconia to aluminum powder is 10:1, and activated aluminum is obtained after ball milling pink;
[0031] Zeolite-AlN / SiO 2 Preparation of nanoparticles: After the activated aluminum powder, zeolite, 40g of silicon dioxide, 10g of lithium hydroxide monohydrate, and 30g of polyetheretherketone particles are mixed uniformly by mechanical stirring, they are put into a high-te...
Embodiment 2
[0032] Example 2: Zeolite-AlN / SiO 2 Preparation of nanoparticles two:
[0033] This implementation prepares zeolite-AlN / SiO 2The steps for nanoparticles are as follows:
[0034] Zeolite modification: roast 100g of zeolite at a temperature of 330°C for 45 minutes, take it out and cool it, then put it into 38wt% hydrochloric acid solution and heat it to reflux for 7 hours, take it out, wash it, dry it, and set it aside;
[0035] Activation of aluminum powder: 120g of aluminum powder and zirconia are milled in an argon atmosphere at a low temperature and high-energy ball for 25 hours at 6°C, the ball milling speed is 500rpm, the mass ratio of zirconia to aluminum powder is 10:1, and activated aluminum is obtained after ball milling pink;
[0036] Zeolite-AlN / SiO 2 Preparation of nanoparticles: After the activated aluminum powder, zeolite, 40g of silicon dioxide, 10g of lithium hydroxide monohydrate, and 30g of polyetheretherketone particles are mixed uniformly by mechanical s...
Embodiment 3
[0037] Example 3: Zeolite-AlN / SiO 2 Preparation of nanoparticles three:
[0038] This implementation prepares zeolite-AlN / SiO 2 The steps for nanoparticles are as follows:
[0039] Zeolite modification: roast 100g of zeolite at 350°C for 30 minutes, take it out and cool it, then put it into 40wt% hydrochloric acid solution and heat it to reflux for 6 hours, take it out, wash it, dry it, and set it aside;
[0040] Activation of aluminum powder: 120g of aluminum powder and zirconia are milled in an argon atmosphere at a low temperature and high-energy ball for 30 hours at 10°C, the ball milling speed is 500rpm, and the mass ratio of zirconia to aluminum powder is 10:1, and activated aluminum is obtained after ball milling pink;
[0041] Zeolite-AlN / SiO 2 Preparation of nanoparticles: After the activated aluminum powder, zeolite, 40g of silicon dioxide, 10g of lithium hydroxide monohydrate, and 30g of polyetheretherketone particles are mixed uniformly by mechanical stirring, ...
PUM
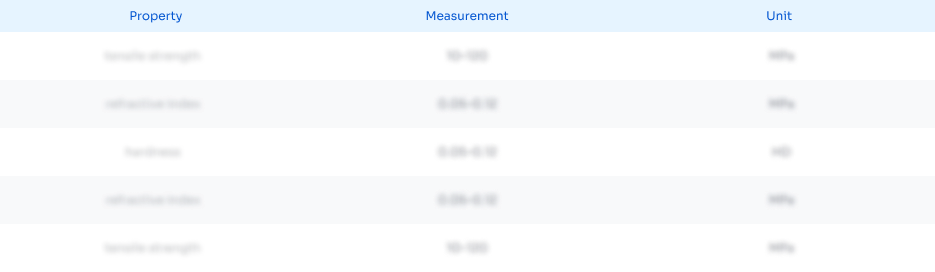
Abstract
Description
Claims
Application Information

- R&D
- Intellectual Property
- Life Sciences
- Materials
- Tech Scout
- Unparalleled Data Quality
- Higher Quality Content
- 60% Fewer Hallucinations
Browse by: Latest US Patents, China's latest patents, Technical Efficacy Thesaurus, Application Domain, Technology Topic, Popular Technical Reports.
© 2025 PatSnap. All rights reserved.Legal|Privacy policy|Modern Slavery Act Transparency Statement|Sitemap|About US| Contact US: help@patsnap.com