A kind of preparation method of high flux composite polyamide reverse osmosis membrane
A composite polyamide and reverse osmosis membrane technology, applied in the direction of reverse osmosis, semi-permeable membrane separation, chemical instruments and methods, etc., can solve the problems of difficult application, sacrifice of membrane desalination rate, etc., to improve water permeability and save costs , the effect of simple operation
- Summary
- Abstract
- Description
- Claims
- Application Information
AI Technical Summary
Problems solved by technology
Method used
Examples
Embodiment 1
[0041] The anti-osmosis membrane production method is as follows:
[0042] 1. Preparation of a polysulfone support base film: 85 g of polysulfone, 0.5 g of polyvinylpyrrolidone is added to 414.5 g n, N-dimethylformamide (DMF) in a stirred state, and the remaining operation is the same. 1;
[0043] 2, formulation of the aqueous phase fluid: the same ratio 1;
[0044] 3, formulation of oil phase solution: the same ratio 1;
[0045] 4, the film formation method is the same as the proportion 1.
[0046] The diaphragm detecting method is the same as a comparison 1, and the results are shown in Table 1.
Embodiment 2
[0048] The anti-osmosis membrane production method is as follows:
[0049] 1. Preparation of a polysulfone support base film: 75 g of polysulfone, 5 g of polyethylene glycol is added to 420 g n, N-dimethylformamide (DMF) in a stirred state, and the remaining operation is the same. 1;
[0050] 2, formulation of the aqueous phase fluid: the same ratio 1;
[0051] 3, formulation of oil phase solution: the same ratio 1;
[0052] 4, the film formation method is the same as the proportion 1.
[0053] The diaphragm detecting method is the same as a comparison 1, and the results are shown in Table 1.
Embodiment 3
[0055] The anti-osmosis membrane production method is as follows:
[0056] 1. Preparation of a polysulfone support base film: 70 g of polysulfone, 1.5 g of polyethylene glycol in a stirred state of 428.5 gn, N-dimethylformamide (DMF), and the remaining operation is the same. 1;
[0057] 2, formulation of the aqueous phase fluid: the same ratio 1;
[0058] 3, formulation of oil phase solution: the same ratio 1;
[0059] 4, the film formation method is the same as the proportion 1.
[0060] The diaphragm detecting method is the same as a comparison 1, and the results are shown in Table 1.
PUM
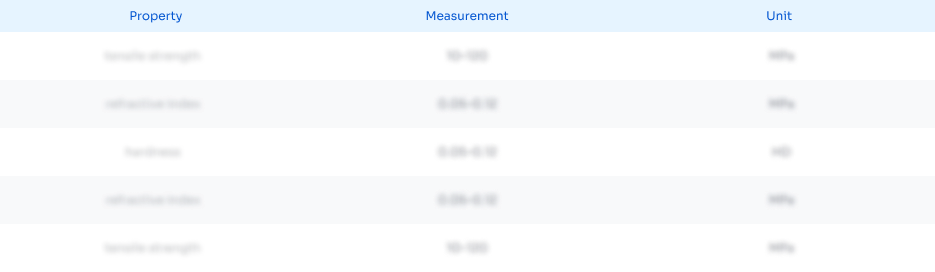
Abstract
Description
Claims
Application Information

- R&D Engineer
- R&D Manager
- IP Professional
- Industry Leading Data Capabilities
- Powerful AI technology
- Patent DNA Extraction
Browse by: Latest US Patents, China's latest patents, Technical Efficacy Thesaurus, Application Domain, Technology Topic, Popular Technical Reports.
© 2024 PatSnap. All rights reserved.Legal|Privacy policy|Modern Slavery Act Transparency Statement|Sitemap|About US| Contact US: help@patsnap.com