Steering load simulator and steering system test method
A load simulation and steering system technology, which is applied in the direction of vehicle steering/bump performance, can solve the problems of difficult to guarantee the accuracy of the load simulation system and low service life, and achieve the effects of reliable data, improved service life, and favorable load force accuracy
- Summary
- Abstract
- Description
- Claims
- Application Information
AI Technical Summary
Problems solved by technology
Method used
Image
Examples
Embodiment 1
[0034] Such as figure 1 As shown, the steering load simulation device provided by the embodiment of the present invention includes: a linkage 1, a steering drive 2 and a brake 3, the steering drive 2 is used to drive the linkage 1 to move; the brake 3 is used to friction brake the linkage 1 , to hinder the movement of linkage 1.
[0035] Specifically, the linkage 1 is used to connect the steering system, and transmit the driving force of the steering system to the steering drive 2; the steering drive 2 moves relative to the brake 3 under the drive of the linkage 1, and the brake 3 is braked by friction. The brake 3 can adopt the electronic parking system, which replaces the hydraulic cylinder, hydraulic valve, hydraulic pump station and complex hydraulic circuit, greatly realizes the simplification of the system and avoids the exhaust during the system installation process. The problem of air bubbles can avoid system instability due to impurities mixed in the oil, and the sys...
Embodiment 2
[0048] The steering system test method provided in the embodiment of the present invention uses the steering load simulation device provided in Embodiment 1, and the steering system test method includes the following steps:
[0049] Calculate the theoretical value of the steering system load at the preset vehicle speed according to the preset vehicle speed;
[0050] Calculate the braking force of the brake 3 according to the theoretical value of the steering system load;
[0051] The control brake 3 loads the linkage 1 . Wherein, calculating the theoretical value of the steering system load at the preset vehicle speed according to the preset vehicle speed includes that the controller 5 inquires the theoretical value of the steering system load at the preset vehicle speed according to the preset vehicle speed, and the steering system load at each vehicle speed. Theoretical values can be known through previous experiments and stored in the memory in advance for the controller...
PUM
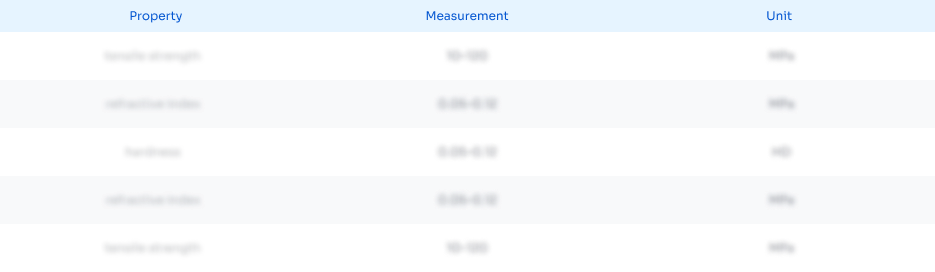
Abstract
Description
Claims
Application Information

- Generate Ideas
- Intellectual Property
- Life Sciences
- Materials
- Tech Scout
- Unparalleled Data Quality
- Higher Quality Content
- 60% Fewer Hallucinations
Browse by: Latest US Patents, China's latest patents, Technical Efficacy Thesaurus, Application Domain, Technology Topic, Popular Technical Reports.
© 2025 PatSnap. All rights reserved.Legal|Privacy policy|Modern Slavery Act Transparency Statement|Sitemap|About US| Contact US: help@patsnap.com