Electronic grade polysilicon reduction furnace base plate and reduction furnace
A polysilicon and reduction furnace technology, applied in the fields of silicon compounds, inorganic chemistry, chemical instruments and methods, etc., can solve the problems of low specific gravity of high-quality electronic-grade polysilicon, uneven temperature distribution on the surface of the silicon core, and high unit energy consumption of products. To achieve the effect of reducing unit energy consumption, reducing formation probability, location and quantity diversification
- Summary
- Abstract
- Description
- Claims
- Application Information
AI Technical Summary
Problems solved by technology
Method used
Image
Examples
Embodiment 1
[0037] Such as figure 1 As shown, the polysilicon reduction furnace of this embodiment includes: a base plate 1 having a disc structure, and a first electrode ring 3, a first air inlet ring 4, a second electrode ring 5, and a first air outlet formed on the base plate 1. Ring 6; Among them, the first electrode ring 3, the first inlet ring 4, the second electrode ring 5 and the first outlet ring 6 are all concentric circles with the center of the chassis 1 as the center and set in sequence from the inside to the outside; Three pairs of electrodes 8 are uniformly arranged on one electrode ring 3, and six pairs of electrodes 8 are uniformly arranged on the second electrode ring 5; 6 mixed gas outlets 7 are uniformly arranged clockwise on the circumference of the first gas outlet ring 6.
[0038] On the circumference of the first air inlet ring 4, 6 mixed gas inlet nozzles are evenly arranged clockwise. The 6 mixed gas inlet nozzles are the first mixed gas inlet nozzle 7'and the second...
Embodiment 2
[0042] Such as figure 2 As shown, the polysilicon reduction furnace of this embodiment includes: a base plate 1 having a disc structure, and a first electrode ring 3, a first air inlet ring 4, a second electrode ring 5, and a first air outlet formed on the base plate 1. Ring 6; Among them, the first electrode ring 3, the first inlet ring 4, the second electrode ring 5 and the first outlet ring 6 are all concentric circles with the center of the chassis 1 as the center and set in order from the inside to the outside; Three pairs of electrodes 8 are uniformly arranged on one electrode ring 3, and six pairs of electrodes 8 are uniformly arranged on the second electrode ring 5; 4 mixed gas outlets 7 are uniformly arranged clockwise on the circumference of the first gas outlet ring 6.
[0043] On the circumference of the first inlet ring 4, there are 8 mixed gas inlet nozzles evenly arranged in a clockwise direction. The 8 mixed gas inlet nozzles are the No. 1 mixed gas inlet nozzle 7...
Embodiment 3
[0047] Such as image 3 As shown, the polysilicon reduction furnace of this embodiment includes: a base plate 1 with a disc structure and a second air inlet ring 2, a first electrode ring 3, a first air inlet ring 4, and a second air inlet ring 2 formed on the base plate 1. The electrode ring 5 and the first air outlet ring 6; wherein, the second air inlet ring 2 is provided with only one inlet nozzle 7'located in the center of the chassis 1, and the nozzle diameter of the inlet nozzle 7'is c; the first electrode ring 3. The first air inlet ring 4, the second electrode ring 5, and the first air outlet ring 6 are all concentric circles with the center of the chassis 1 as the center and are arranged in sequence from the inside to the outside; the first electrode ring 3 is evenly arranged with three For the electrodes 8, the second electrode ring 5 is evenly arranged with six pairs of electrodes 8; on the circumference of the first gas outlet ring 6 there are 6 mixed gas outlets 7 ...
PUM
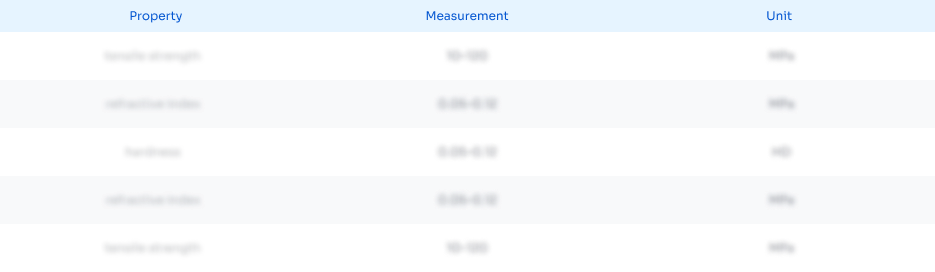
Abstract
Description
Claims
Application Information

- R&D
- Intellectual Property
- Life Sciences
- Materials
- Tech Scout
- Unparalleled Data Quality
- Higher Quality Content
- 60% Fewer Hallucinations
Browse by: Latest US Patents, China's latest patents, Technical Efficacy Thesaurus, Application Domain, Technology Topic, Popular Technical Reports.
© 2025 PatSnap. All rights reserved.Legal|Privacy policy|Modern Slavery Act Transparency Statement|Sitemap|About US| Contact US: help@patsnap.com