Metal workpiece processing method embedded with preform
A processing method and technology for metal workpieces, applied in 3D printing-related fields, can solve problems such as cracking, pipe blockage, and low dimensional accuracy in complex local areas, and achieve the effects of widening the range of material selection, optimizing manufacturing accuracy, and improving printing efficiency
- Summary
- Abstract
- Description
- Claims
- Application Information
AI Technical Summary
Problems solved by technology
Method used
Image
Examples
Embodiment 1
[0057] Fig. 4 is a schematic diagram of the manufacturing process of an injection mold with a conformal cooling water channel without dividing the matrix region, wherein Figure 4a 3D model for the conformal cooling channel as a prefab, Figure 4b For an injection mold with conformal cooling channels, the specific steps are as follows:
[0058] (1) First design the model of the mold, and divide the model into a prefabricated part area and a printing area. Then divide the printing area into a front printing area smaller than the height of the plane where the preform is located and a rear printing area greater than the height of the plane where the preform is located, and design a positioning groove on the model of the front printing area to obtain the target front printing area;
[0059] (2) Select a suitable molding process to prepare the prefabricated part according to the geometric dimensions and structural features of the prefabricated part; in this embodiment, for the co...
Embodiment 2
[0065] Fig. 5 is a schematic diagram of the manufacturing process of a stamping punch with a conformal cooling channel divided into a matrix area, wherein Figure 5a It is a conformal cooling channel preform fixed on the base plate, Figure 5b To form a stamping punch with a conformal cooling channel, the specific steps are as follows:
[0066] (1) First design the model of the stamping punch, and divide the model area into three parts: the matrix area, the prefabricated part area and the printing area.
[0067] (2) First, according to the geometric dimensions and structural characteristics of the conformal cooling water channel prefabricated part, an appropriate molding process is selected to prepare the conformal cooling water channel prefabricated part; The base area of the mould, and two positioning holes are machined on the base plate for positioning the conformal cooling water channel preform; the diameter of the positioning holes is slightly larger than the diameter ...
PUM
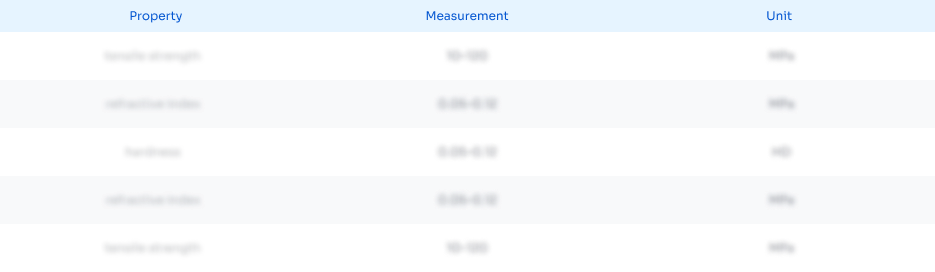
Abstract
Description
Claims
Application Information

- Generate Ideas
- Intellectual Property
- Life Sciences
- Materials
- Tech Scout
- Unparalleled Data Quality
- Higher Quality Content
- 60% Fewer Hallucinations
Browse by: Latest US Patents, China's latest patents, Technical Efficacy Thesaurus, Application Domain, Technology Topic, Popular Technical Reports.
© 2025 PatSnap. All rights reserved.Legal|Privacy policy|Modern Slavery Act Transparency Statement|Sitemap|About US| Contact US: help@patsnap.com