An additional track system with a wheel forward/reverse converter and a wheeled vehicle
A technology of converters and wheels, applied in tracked vehicles, motor vehicles, transportation and packaging, etc., can solve the problems of stress concentration, inconvenience, volume and mass increase, etc., to increase the maximum torque, reduce the volume of the device, and reduce the grounding ratio pressure effect
- Summary
- Abstract
- Description
- Claims
- Application Information
AI Technical Summary
Problems solved by technology
Method used
Image
Examples
Embodiment 1
[0037] Embodiment 1: see Figure 4 , the wheel forward and reverse converter 1 is arranged between the output shaft of the prime mover 4 and the gearbox 13, the sun gear of the wheel forward and reverse converter is connected to the output shaft of the prime mover, the ring gear is connected to the input shaft of the gearbox, and the ring gear is fixed Attached to vehicle chassis.
[0038] see Figure 5 , the three circles in the figure are the pitch circles of the sun gear, planetary gear, and ring gear; a-the pitch circle diameter of the sun gear; b-the pitch circle diameter of the planetary gear; c-the pitch circle diameter of the ring gear. Obviously the moment M acting on the sun gear 1 =F 1 r 1 ;Moment M acting on the ring gear 3 =F 3 r 3 ;Moment M acting on planet carrier H H =F H r H .
[0039] Define the gear ratio of the ring gear and the sun gear as α, that is, α=Z / Z=r / r.
[0040] By gear geometry: r 3 = αr 1 、r H =(r 1 + r 3 ) / 2=r 1 (1+α) / 2.
[0...
Embodiment 2
[0052] Embodiment 2: The wheel forward and reverse converter is arranged after the gearbox and before the differential. The advantages and disadvantages are similar to those of Embodiment 1.
Embodiment 3
[0053] Embodiment 3: The wheel forward and reverse converter is embedded in the wheel hub of the vehicle drive wheel, see Figure 6 , Figure 7 . The wheel reversing device is connected with the crawler track running parts through the wheel-shoe connection assembly 3 with the planet carrier 19 on the upper part. The wheel-shoe connection assembly is a rod-plate truss structure with a triangular layout in general. Its top is processed with a ring, and a shaft hole for installing the planetary wheel shaft is opened on the ring, which acts as a planet carrier. The bottom of the connecting assembly is fixedly connected with the crawler frame. The sun gear 16 in the wheel forward and reverse converter is fixedly connected with the vehicle transmission half shaft 15, the ring gear 17 is fixedly connected with the rim, and the track frame is connected with the vehicle chassis through a metal chain. Tightly limit further tilting and play the role of anti-tilting mechanism. This em...
PUM
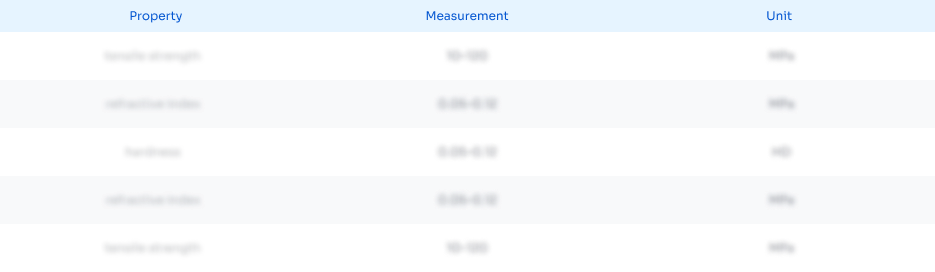
Abstract
Description
Claims
Application Information

- Generate Ideas
- Intellectual Property
- Life Sciences
- Materials
- Tech Scout
- Unparalleled Data Quality
- Higher Quality Content
- 60% Fewer Hallucinations
Browse by: Latest US Patents, China's latest patents, Technical Efficacy Thesaurus, Application Domain, Technology Topic, Popular Technical Reports.
© 2025 PatSnap. All rights reserved.Legal|Privacy policy|Modern Slavery Act Transparency Statement|Sitemap|About US| Contact US: help@patsnap.com