A crimping process of automobile wire harness
A technology of automotive wiring harnesses and wiring harnesses, applied in the field of wiring harnesses, can solve problems such as poor working conditions of wiring harnesses, increased overall loss, loose connections, etc., and achieve the effect of reducing production costs
- Summary
- Abstract
- Description
- Claims
- Application Information
AI Technical Summary
Problems solved by technology
Method used
Examples
Embodiment Construction
[0017] The technical solutions in the embodiments of the present invention will be clearly and completely described below in conjunction with the embodiments of the present invention. Apparently, the described embodiments are only some of the embodiments of the present invention, not all of them. Based on the embodiments of the present invention, all other embodiments obtained by persons of ordinary skill in the art without making creative efforts belong to the protection scope of the present invention.
[0018] Embodiment A crimping process of an automobile wiring harness, using stamping equipment to crimp the wiring terminal and the automobile wiring harness body together, including the following process steps:
[0019] (1) Deoxidize the wire harness after the wire is opened, and then dry it at high temperature after deoxidization;
[0020] (2) First use the coarse adjustment lever to adjust the overall crimping height, and then use the fine adjustment lever to slightly adju...
PUM
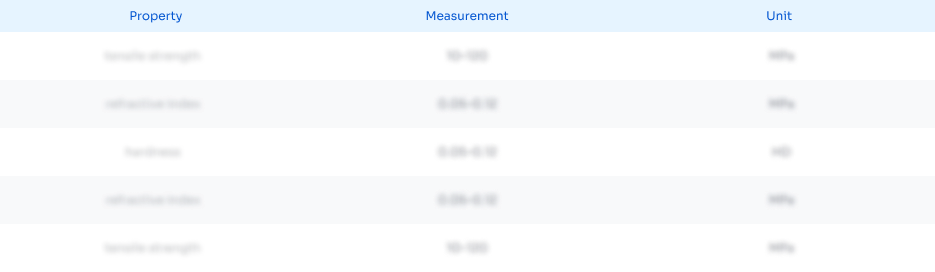
Abstract
Description
Claims
Application Information

- R&D
- Intellectual Property
- Life Sciences
- Materials
- Tech Scout
- Unparalleled Data Quality
- Higher Quality Content
- 60% Fewer Hallucinations
Browse by: Latest US Patents, China's latest patents, Technical Efficacy Thesaurus, Application Domain, Technology Topic, Popular Technical Reports.
© 2025 PatSnap. All rights reserved.Legal|Privacy policy|Modern Slavery Act Transparency Statement|Sitemap|About US| Contact US: help@patsnap.com