A method for manufacturing a transformer core and a transformer core manufacture device for realizing the method
A transformer core and manufacturing method technology, applied in the direction of inductance/transformer/magnet manufacturing, transformer/inductance parts, electrical components, etc., can solve the problems of long transformer core production cycle and low production efficiency, and shorten production cycle, increase production efficiency, and reduce noise
- Summary
- Abstract
- Description
- Claims
- Application Information
AI Technical Summary
Problems solved by technology
Method used
Image
Examples
Embodiment Construction
[0022] Embodiments of the present invention will be further described below in conjunction with the accompanying drawings.
[0023] A specific embodiment of the transformer core manufacturing device of the present invention, such as Figure 1 to Figure 6 As shown, the transformer iron core manufacturing device includes a stacking station 6 for stacking iron chips. The stacking station 6 is provided with a stacking position 61 for stacking the iron chips and a stacking station for the iron core after the iron core 4 is bound. Standing up position 62. The transformer iron core manufacturing device also includes a binding device for binding the stacked iron cores and an iron core column clamp for clamping the iron core column before the iron core binding. The binding device includes a binding force measuring operation wrench 5, The band binding technology belongs to the prior art, and will not be repeated here. The strap force measuring operation wrench 5 is used to bind the st...
PUM
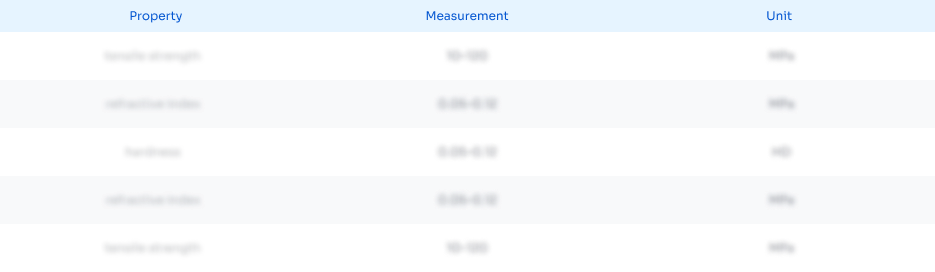
Abstract
Description
Claims
Application Information

- R&D Engineer
- R&D Manager
- IP Professional
- Industry Leading Data Capabilities
- Powerful AI technology
- Patent DNA Extraction
Browse by: Latest US Patents, China's latest patents, Technical Efficacy Thesaurus, Application Domain, Technology Topic.
© 2024 PatSnap. All rights reserved.Legal|Privacy policy|Modern Slavery Act Transparency Statement|Sitemap