Shift range control device
A control device and gear technology, applied in the direction of electronic reversing motor control, control system, stop device, etc., can solve problems such as fluctuations
- Summary
- Abstract
- Description
- Claims
- Application Information
AI Technical Summary
Problems solved by technology
Method used
Image
Examples
no. 1 Embodiment approach
[0026] exist Figure 1 to Figure 6 The shift position control device according to the first embodiment of the present disclosure is shown.
[0027] like figure 1 and figure 2 As shown, the shift-by-wire system 1 includes a motor 10 , a shift position switching mechanism 20 , a parking lock mechanism 30 , a shift position control device 40 , and the like.
[0028] The motor 10 is powered by a battery 45 (refer to image 3 ) is rotated by being supplied with electric power, and functions as a driving source of the shift position switching mechanism 20 . As the motor 10 , a motor capable of changing the magnitude of the current through feedback control and changing the command for each phase can be used. The motor 10 of this embodiment is a permanent magnet type DC brushless motor. like image 3 As shown, the motor 10 has two sets of winding wires 11 , 12 . The first winding wire group 11 has a U1 coil 111 , a V1 coil 112 , and a W1 coil 113 . The second winding wire gro...
no. 2 Embodiment approach
[0091] exist Figure 7 , Figure 8A as well as Figure 8B The second embodiment of the present disclosure is shown in . In this embodiment, since the switching control process is different from the above-described embodiment, the description will focus on this point.
[0092] based on Figure 7 The shown flowchart describes the switching control process of this embodiment.
[0093] The processing of S201~S204 and Figure 5 The processing of S101 to S104 is the same.
[0094] In S205, the switching control unit 65 determines whether or not the angular deviation e is larger than the first angle determination threshold e_th1. The first angle determination threshold e_th1 is set to correspond to a value (for example, 1° in terms of mechanical angle) that does not cause overshoot when the motor speed Msp is large, even when the motor 10 is stopped from its high-speed rotation state. count value of . The first angle determination threshold e_th1 is set to a value larger than...
PUM
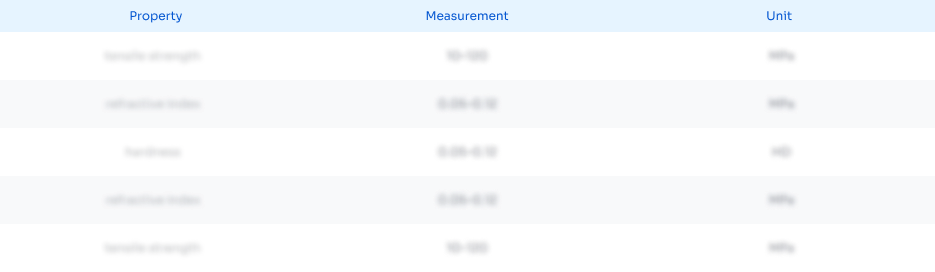
Abstract
Description
Claims
Application Information

- R&D
- Intellectual Property
- Life Sciences
- Materials
- Tech Scout
- Unparalleled Data Quality
- Higher Quality Content
- 60% Fewer Hallucinations
Browse by: Latest US Patents, China's latest patents, Technical Efficacy Thesaurus, Application Domain, Technology Topic, Popular Technical Reports.
© 2025 PatSnap. All rights reserved.Legal|Privacy policy|Modern Slavery Act Transparency Statement|Sitemap|About US| Contact US: help@patsnap.com