Simulation test piece and simulation design method for blade root portion of turbine
A simulation test and impeller technology, applied in the testing of mechanical components, testing of machine/structural components, testing of elasticity, etc., can solve the problem of scarcity of blade root simulation test piece design, and achieve the effect of facilitating machining
- Summary
- Abstract
- Description
- Claims
- Application Information
AI Technical Summary
Problems solved by technology
Method used
Image
Examples
Embodiment Construction
[0020] Such as figure 1 As shown, the simulated test piece involved in the present invention is composed of two upper and lower loading sections 1 , a pair of parallel metal plates 2 and a vertical metal plate 3 . The loading section 1 is located at both ends of the simulated test piece, perpendicular to the parallel metal plate 2, and connected by the transition fillet 4 of the loading section; the vertical metal plate 3 is located between the two parallel metal plates 2, and has a certain distance from the central axis of the loading section 1. Deviating, connected by the transition fillet 5 of the test section. Side-by-side pin holes 6 are arranged on the upper and lower loading sections 1 for connecting with the fixture. The loading section 1 and the vertical metal plate 3 are perpendicular to each other. Among them, the vertical metal plate 3 simulates the turbine blade, and the transition fillet 5 of the test section simulates the root of the blade, which is the observ...
PUM
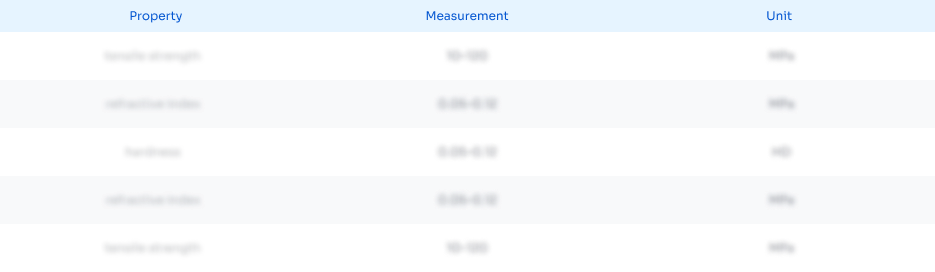
Abstract
Description
Claims
Application Information

- Generate Ideas
- Intellectual Property
- Life Sciences
- Materials
- Tech Scout
- Unparalleled Data Quality
- Higher Quality Content
- 60% Fewer Hallucinations
Browse by: Latest US Patents, China's latest patents, Technical Efficacy Thesaurus, Application Domain, Technology Topic, Popular Technical Reports.
© 2025 PatSnap. All rights reserved.Legal|Privacy policy|Modern Slavery Act Transparency Statement|Sitemap|About US| Contact US: help@patsnap.com