Layering control method in carbon fiber machining process
A process and layered control technology, applied in metal processing equipment, manufacturing tools, grinding machines, etc., can solve the problems of high cost and low processing efficiency, and achieve reduced cutting force, reduced processing layering, and good layered control effect. Effect
- Summary
- Abstract
- Description
- Claims
- Application Information
AI Technical Summary
Problems solved by technology
Method used
Image
Examples
Embodiment Construction
[0022] Through the following examples, in conjunction with the accompanying drawings, the technical solution of the present invention is further specifically described. The method of the present invention controls the carbon fiber material in the processing process by adopting suitable processing equipment, reasonable processing parameters and variable feed processing methods. stratification, such as figure 1 Shown, is the ultrasonic processing machine tool that the present invention adopts, comprises machine tool main shaft 1, ultrasonic generator 2, horn 3, cutting tool 4, fixture 5, processing platform 6, processing material 7 and ultrasonic power supply 8, on machine tool main shaft 1 The ultrasonic generator 2, the horn 3 and the tool 4 are respectively installed from top to bottom. The ultrasonic generator 2, the horn 3 and the tool 4 rotate together with the machine tool spindle 1 at high speed. On the platform 6, a tooling fixture 5 specially used for positioning and c...
PUM
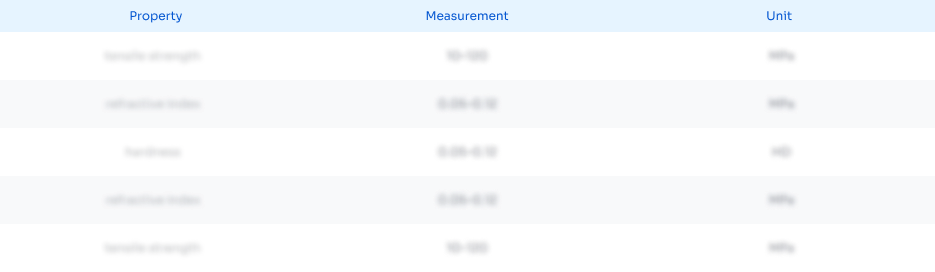
Abstract
Description
Claims
Application Information

- R&D
- Intellectual Property
- Life Sciences
- Materials
- Tech Scout
- Unparalleled Data Quality
- Higher Quality Content
- 60% Fewer Hallucinations
Browse by: Latest US Patents, China's latest patents, Technical Efficacy Thesaurus, Application Domain, Technology Topic, Popular Technical Reports.
© 2025 PatSnap. All rights reserved.Legal|Privacy policy|Modern Slavery Act Transparency Statement|Sitemap|About US| Contact US: help@patsnap.com