Control method of multi-cavity steel component assembling and positioning mechanism
A positioning mechanism and control method technology, applied in auxiliary devices, manufacturing tools, auxiliary welding equipment, etc., can solve problems such as large positioning deviations, achieve the effects of preventing false welding, compact structure, and shortening the processing period
- Summary
- Abstract
- Description
- Claims
- Application Information
AI Technical Summary
Problems solved by technology
Method used
Image
Examples
Embodiment
[0032] Example: such as Figure 1-5 As shown, a control method of a multi-cavity steel member assembly positioning mechanism is as follows:
[0033] Step 1: hoist the bottom plate 9 onto the working platform by driving, and at the same time place the square tubes 6 on both sides on the working platform to be in close contact with the sides of the bottom plate 9, and then use the square tube to position and assemble the component 4 and the upper tube to position the pressing piece 7 The other side tube is compressed and positioned.
[0034] Step 2: hoist the steel bar truss 13 on the positioned bottom plate 9, and provide preliminary positioning assistance to the steel bar truss 13 through the steel bar truss assembly and positioning component 1. The rack guide rail 15 drives the end preliminary positioning member 11 to move laterally on the end preliminary positioning member guide rail 14 to assist in positioning the steel bar truss.
[0035] The third step: the positioning ...
PUM
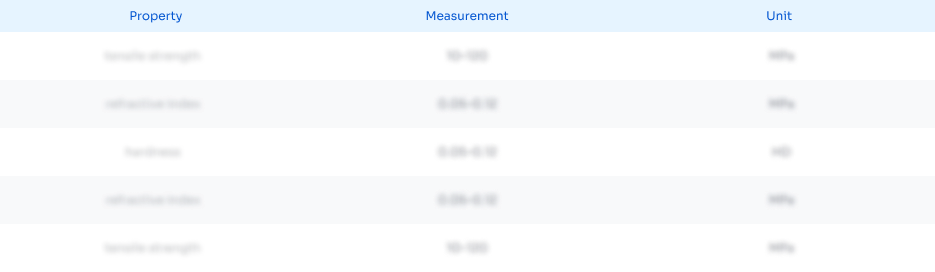
Abstract
Description
Claims
Application Information

- R&D
- Intellectual Property
- Life Sciences
- Materials
- Tech Scout
- Unparalleled Data Quality
- Higher Quality Content
- 60% Fewer Hallucinations
Browse by: Latest US Patents, China's latest patents, Technical Efficacy Thesaurus, Application Domain, Technology Topic, Popular Technical Reports.
© 2025 PatSnap. All rights reserved.Legal|Privacy policy|Modern Slavery Act Transparency Statement|Sitemap|About US| Contact US: help@patsnap.com