Method for synthesizing Al4O4C nanometer particle reinforced aluminum matrix composite material in situ
An in-situ synthesis and nanoparticle technology, applied in the field of composite materials, can solve the problems of poor combination of matrix and reinforcement phase particles, easy contamination of the interface, and limited mechanical properties, and achieve low cost, uniform and compact structure, and good mechanical properties. Effect
- Summary
- Abstract
- Description
- Claims
- Application Information
AI Technical Summary
Problems solved by technology
Method used
Image
Examples
Embodiment 1
[0031] (1) Clean and preheat the steel components used in the experiment. Derust, grind and clean the steel molds used in the casting process, the colander for removing impurities, the steel nozzles for degassing operation, and the molds, etc., and put them in a 120°C resistance furnace for heating and drying for 1 hour, take them out and cool them Install the argon degassing nozzle; clean the graphite crucible, remove the impurities falling off the surface and dry it to remove water.
[0032] (2) Prepare raw materials: mix pure aluminum ingots and pure silicon ingots according to the mass percentage of 99:1, and the introduction amount of phenolic resin is 0.1wt% of the total mass of pure aluminum ingots and pure silicon ingots.
[0033] (3) Melting: Put pure aluminum ingots and pure silicon ingots into graphite crucibles in medium-frequency induction metal melting furnaces and heat them to 850°C to 900°C to completely melt, then remove impurities on the surface of molten alu...
Embodiment 2
[0038] (1) Clean and preheat the steel components used in the experiment. Derust, grind and clean the steel molds used in the casting process, the colander for removing impurities, the steel nozzles for degassing operation, and the molds, etc., and put them in a 120°C resistance furnace for heating and drying for 1 hour, take them out and cool them Install the argon degassing nozzle; clean the graphite crucible, remove the impurities falling off the surface and dry it to remove water.
[0039] (2) Prepare raw materials: mix pure aluminum ingots and pure silicon ingots according to the mass percentage of 83:17, and the introduction amount of phenolic resin is 3wt% of the total mass of pure aluminum ingots and pure silicon ingots.
[0040] (3) Melting: Put pure aluminum ingots and pure silicon ingots into graphite crucibles in medium-frequency induction metal melting furnaces and heat them to 850°C to 900°C to completely melt, then remove impurities on the surface of molten alum...
Embodiment 3
[0045] (1) Clean and preheat the steel components used in the experiment. Derust, grind and clean the steel molds used in the casting process, the colander for removing impurities, the steel nozzles for degassing operation, and the molds, etc., and put them in a 120°C resistance furnace for heating and drying for 1 hour, take them out and cool them Install the argon degassing nozzle; clean the graphite crucible, remove the impurities falling off the surface and dry it to remove water.
[0046](2) Prepare raw materials: mix pure aluminum ingots and pure silicon ingots according to the mass percentage of 75:25, and the introduction amount of phenolic resin is 6wt% of the total mass of pure aluminum ingots and pure silicon ingots.
[0047] (3) Melting: Put pure aluminum ingots and pure silicon ingots into graphite crucibles in medium-frequency induction metal melting furnaces and heat them to 850°C to 900°C to completely melt, then remove impurities on the surface of molten alumi...
PUM
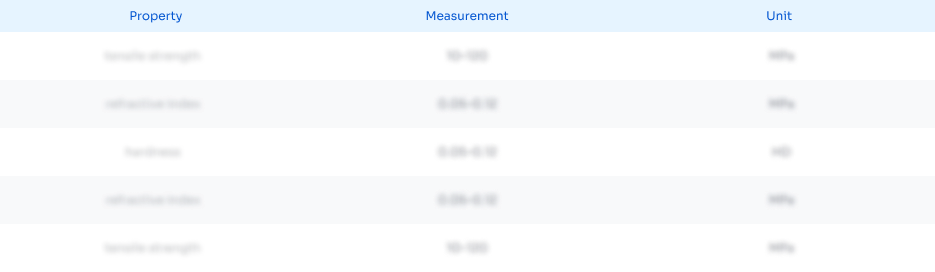
Abstract
Description
Claims
Application Information

- R&D
- Intellectual Property
- Life Sciences
- Materials
- Tech Scout
- Unparalleled Data Quality
- Higher Quality Content
- 60% Fewer Hallucinations
Browse by: Latest US Patents, China's latest patents, Technical Efficacy Thesaurus, Application Domain, Technology Topic, Popular Technical Reports.
© 2025 PatSnap. All rights reserved.Legal|Privacy policy|Modern Slavery Act Transparency Statement|Sitemap|About US| Contact US: help@patsnap.com