Preparation method of mask interlayer interlayer filter material
A filter material and interlayer technology, which is applied in the field of preparation of interlayer filter materials in masks, can solve problems such as difficulty in realizing high-efficiency and low-resistance filtration, and achieve the effects of controllable fiber morphology, rich pore structure, and high porosity.
- Summary
- Abstract
- Description
- Claims
- Application Information
AI Technical Summary
Problems solved by technology
Method used
Examples
Embodiment 1
[0016] A preparation method for interlayer filter material in the middle of a mask, comprising the following steps:
[0017] S1. Use chopped plant fiber to configure fiber slurry and add it to the refiner for refining treatment. The rotating speed of the refining is 15000r, and then sieve with a fiber sieving instrument. The selection of the screen mesh is 300um, and the sieved After the solution is concentrated to a concentration of 20wt%, the fibrillated plant fiber solution is obtained;
[0018] S2. Prepare a sodium alginate solution with a concentration of 3wt% and a PVA solution with a concentration of 20wt%, respectively, prepare the fibrillated plant fiber solution in step S1, and mix the sodium alginate solution and the PVA solution in a mass ratio of 1:1:1 , and then add oxidized activated carbon, the content of oxidized activated carbon is 8wt%, let stand defoaming, obtain composite solution, then pour in the container, cast into the hydrogel film that thickness is 1...
Embodiment 2
[0023] A preparation method for interlayer filter material in the middle of a mask, comprising the following steps:
[0024] S1. Use chopped plant fibers to configure fiber slurry and add it to the refiner for refining treatment. The rotating speed of the refining is 20000r, and then sieve with a fiber sieving instrument. The selection of the sieve mesh is 150um, and the sieved After the solution is concentrated to a concentration of 25wt%, the fibrillated plant fiber solution is obtained;
[0025] S2. Prepare a sodium alginate solution with a concentration of 6wt% and a PVA solution with a concentration of 10wt%, respectively, prepare a fibrillated plant fiber solution in step S1, and mix the sodium alginate solution and the PVA solution in a mass ratio of 1:1:1 , and then add oxidized activated carbon, the content of oxidized activated carbon is 4wt%, leave standstill defoaming, obtain composite solution, then pour in the container, cast into the hydrogel film that thickness...
Embodiment 3
[0030] A preparation method for interlayer filter material in the middle of a mask, comprising the following steps:
[0031] S1. Use chopped plant fiber to configure fiber slurry and add it to the refiner for refining treatment. The rotating speed of the refining is 16000r, and then sieve with a fiber sieving instrument. The selection of the screen mesh is 180um, and the sieved After the solution is concentrated to a concentration of 22wt%, the fibrillated plant fiber solution is obtained;
[0032] S2. Prepare a sodium alginate solution with a concentration of 4wt% and a PVA solution with a concentration of 18wt%, respectively, prepare the fibrillated plant fiber solution in step S1, and mix the sodium alginate solution and the PVA solution in a mass ratio of 1:1:1 , then add oxidized activated carbon, the content of oxidized activated carbon is 5wt%, leave standstill defoaming, obtain composite solution, then pour in the container, cast into the hydrogel film that thickness i...
PUM
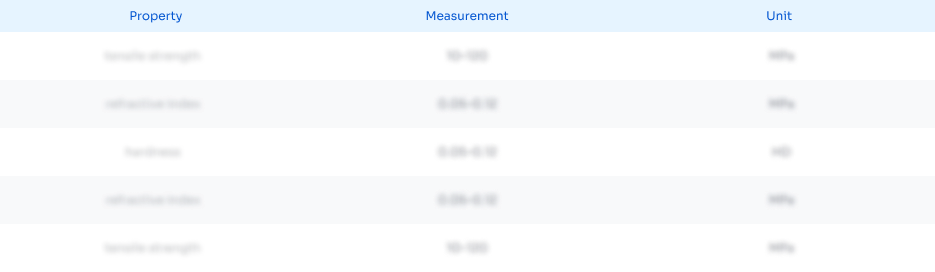
Abstract
Description
Claims
Application Information

- R&D
- Intellectual Property
- Life Sciences
- Materials
- Tech Scout
- Unparalleled Data Quality
- Higher Quality Content
- 60% Fewer Hallucinations
Browse by: Latest US Patents, China's latest patents, Technical Efficacy Thesaurus, Application Domain, Technology Topic, Popular Technical Reports.
© 2025 PatSnap. All rights reserved.Legal|Privacy policy|Modern Slavery Act Transparency Statement|Sitemap|About US| Contact US: help@patsnap.com