Equipment and method for preparing ultra-thin glass by utilizing glass fiber melting furnace discharge materials
A glass fiber and thin glass technology, which is applied in glass manufacturing equipment, glass forming, vertical drawing of glass liquid, etc. problems, to achieve the effect of improving comprehensive utilization efficiency, high utilization value, and beneficial to popularization and application
- Summary
- Abstract
- Description
- Claims
- Application Information
AI Technical Summary
Problems solved by technology
Method used
Image
Examples
Embodiment
[0033] like Figure 1-2 As shown, a device for preparing ultra-thin flexible glass using the discharge material of a glass fiber melting furnace, which consists of a furnace discharge tank 1, a regulator 2, a glass liquid tank 4, an electric heating system 5, a glass forming tank 6, a vertical drawing The edge machine 7, the first roll 8 for down-drawing, the second thinning roll 9, the heating furnace 10, the third thinning roll 12, the drum 13, the glass fiber protective layer 14, the annealing kiln 15, and the winding roll 16 are composed of parts.
[0034] like Figure 1-2 As shown, the lower end of the furnace discharge pool 1 is provided with a discharge port 3, and the furnace discharge pool 1 is connected with the glass forming tank 6 through the glass liquid tank 4, and the upper side of the glass liquid tank 4 is provided with a regulator 2, and the glass The two sides of the liquid tank 4 are provided with an electric heating system 5, and the two sides of the glas...
PUM
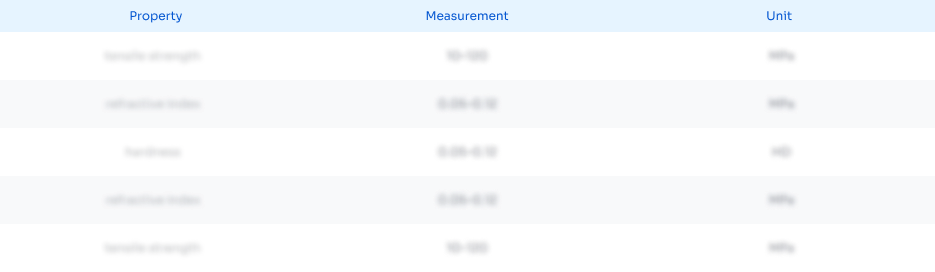
Abstract
Description
Claims
Application Information

- R&D
- Intellectual Property
- Life Sciences
- Materials
- Tech Scout
- Unparalleled Data Quality
- Higher Quality Content
- 60% Fewer Hallucinations
Browse by: Latest US Patents, China's latest patents, Technical Efficacy Thesaurus, Application Domain, Technology Topic, Popular Technical Reports.
© 2025 PatSnap. All rights reserved.Legal|Privacy policy|Modern Slavery Act Transparency Statement|Sitemap|About US| Contact US: help@patsnap.com